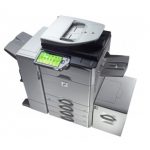
All about printing papers …..3
papers ….. –3–
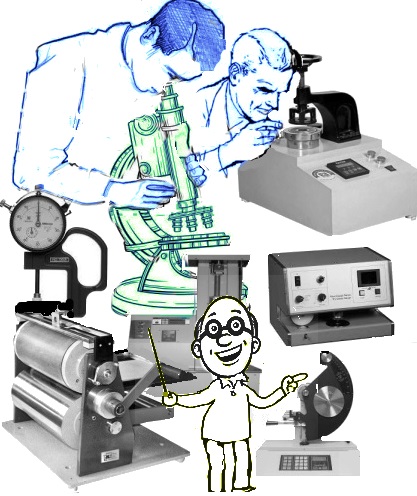
The thickness and weight of the paper (GSM)
Besides cost factor the thickness plays an important role. Heavier or thinner fiber formation determines the thickness which plays an important role in quality of reproduction and appearance of the print material on the paper. Higher the value expressed in terms of GSM, higher will be the thickness of the paper. While the thickness of the paper is tested by a micrometer, the GSM is arrived by weighing one square meter of any thickness of paper to work out the paper lot weight either in reams or reels of specific size and cost worked out. However since the weight and thickness are interlinked, per ream or per 1000 sheets of a specific size paper will have variation per every ream by ± few grams within acceptable limits as permitted internationally due to the manufacturing process.
Tearing resistance
What is tear resistance? It resistance indicates the ability of the paper to withstand tearing force of the paper while handling, that is how fast it can be torn in either direction – machine or cross direction. Machine direction means the direction of the paper web which is running on the machine during paper making. On the other hand Cross direction means the direction which is perpendicular to the paper sheet that is running on the machine during paper making. The tear resistance test demonstrate whether the paper will get easily torn or strong enough to withstand the wear and tear during various acts of usages. Tear resistance also influences the folding process. The paper with less tear resistance is considered to be a weak paper. ISO 1974:2012 specifies a method for determining the (out-of-plane) tear resistance of paper and the most commonly used apparatus to test this factor is Elmendorf Tearing Resistance tester.
Folding strength
Bursting strength
Opacity
The opacity of the paper depends on the extent of fibber content, degree of bleaching of the fibers, and the kind of coating etc. The thickness of the paper also influences the opacity. Remember that the thickness of paper alone is not sufficient to increase the opacity because sometimes even the thinner paper will have more opacity than the thicker paper because of the fiber and filler contents. Opacity in simple term is a measure of a material’s ability to obstruct the passage of light. Sufficient opacity is important to prevent printed text from showing through in a harmful manner on the reverse side of a paper thereby marring the appearance of the print quality. Opacity is measured as the percentage of light absorbed by a sheet of paper. The procedural standards are explained in ISO 2471 and TAPPI T425.
Porosity
Smoothness
Brightness
Surface strength ( for fluff/ debris)
Recycling of waste paper
Most of the paper mills manufacture virgin paper (pure pulp paper) from wood, linen, and cellulose fibbers, last few decades a part of recycled paper too have began to be added in the pulp made, since recycling of used paper as renewable resource has gained momentum which helps environmental protection and pollution control measures.
Recycling of printed and waste paper is the process of collecting and processing material that would otherwise be thrown away as trash or burnt. There are three categories of paper like wastage trimmings and other paper scrap from the paper manufacturing plants itself, unused and paper trimmings from the presses and finally the printed magazines, news papers and other discarded print material. The paper from these three main sources is pooled together and recycled pulp prepared. However in respect of printed papers, by engaging a process called de inking process, in which the printed inks, stains, and glue like material are removed by chemical process without affecting the fibbers on them. Recycling the paper process has many steps involved in them.
Recycled paper pulp prepared from the waste papers as collected from waste locations but they are used only for manufacturing corrugated boards, wrapping papers, and packing papers.
Vide article ‘Need for Waste Paper Recycling in India: How Can It Be Done’ dated January 15, 2015 the author Rumani Saikia Phukan (http://www.mapsofindia.com/my-india/society/need-for-waste-paper-recycling-in-india-how-can-it-be-done) states :
Quote:-
In India more than 550 mills make use of waste paper as the main raw material for making paper, paperboard and for production of newsprint. Waste paper is collected indigenously and also imported. In this country, every year around three million tonnes of waste paper is recovered, which is only about 20% of the total. When we compare this with other countries, the amount is comparatively very low. For instance, developed countries like Germany recovers 73% waste paper, Sweden 69%, Japan 60%, USA 49% etc. Why do we need to recycle paper?
:- Unquote
ISO standards for papers
Standardization of paper became necessary as the printing machineries and equipments used for reproduction on paper can be accordingly designed to accommodate the standard sizes of papers for printing. The other factors that influenced for standardization on paper sizes were:
- to standardise the printed books so that it will help in proper stacking and handling in cupboards
- standardise the use of envelopes for postal transmission
- standardise the record keeping files and for archival purposes
- non standard sizes of printed materials will not only occupy more space in storage but also make it difficult to handle from racks, cupboards and files mainly in Libraries and Archival storage rooms .
The international paper sizes are categorised in three series namely A, B and C. Every part of them are termed as A, B and C with their subdivisions as A‘n’, B‘n’, and C‘n’, the ‘n’ in each of the subdivisions. When the full sized sheet of the specific series is divided into two halves, each halves will have exactly same proportion of area in size compared to the full sheet.
For example when A0 paper which is the biggest in A series which is standardized as one square meter in area (841 mm x 1189 mm) is cut into two equal parts (cut in the side parallel to the shorter side) each halved paper becomes A1 in size each halve having exactly equivalent area. That means when the A series of paper is cut into two halves, you get two perfect, identical pieces of the paper equivalent to the size of the full sheet which was cut. Similarly when A1 is further divided into two equal halves, it becomes A2 and so on till A 5 is reached which is the end in series A paper.
If we have to express it in simple term, it can be expressed that even though the dimensions of the two sheets halved will be different in size than the original sheet from which they were cut, the proportion of their length and width will be always remain constant i.e the ratio between the height and width of a sheet will always be the square root of 2 i.e 1.414 (1189 ÷ 841 = 1.414). The main advantage of this system is that whenever you decide to make copies by enlarging or reducing the original contents of the material including images, text etc they can be reproduced on bigger or smaller sized sheets without losing their symmetry as maintained in the original size sheet.
The ISO system of paper sizes exploit these properties of the aspect ratio and applies to the three series of paper as advocated in ISO standard. What are A, B and C series of paper?
The three ISO standards that govern the paper sizes are classified as ISO 216, ISO 217 and ISO 269 all of which have the same aspect ratio, 1:√2, at least to within the rounding off to whole numbers of millimeters.
While A series of paper is trimmed size, the B series papers are slightly bigger than A series paper. It is needed in certain cases of reproduction where the images are to touch the edges (bleed off) and after printing, when the sheets are trimmed it comes down to the exact A series size. The ISO standard applicable for trimmed paper- A series- is ISO 216.
Certain jobs may require printing to be done up to the last edges on sheets and therefore to provide margin for the grippers on the machines during printing and to provide enough margin for bleed off images till the edges extra small margin will be required. This allows printed images remain up to the edges of the books/ magazines/ sheets even after after they are trimmed to required size. Ultimately the print material will be cut to match the A format.
ISO 217 specifies a primary range and a supplementary range of untrimmed sizes of paper in B series. The untrimmed sizes are RA and SRA which are trimmed to the ISO-A series of sizes. It also specifies the method for the indication of the machine direction for trimmed sheets. RA (Raw format of A) size which is 105 % of A series paper and SRA (Supplementary Raw format of A) which is 115 % of A series paper are untrimmed sizes of paper to achieve ultimate requirement of A series papers.
The C series sizes are to accommodate the standard sizes of envelopes of A and B series of paper. This is also based on the square root 2 aspect ratio. ISO 269 defines several standard envelope sizes, which are designed for use with ISO 216 standard paper sizes.
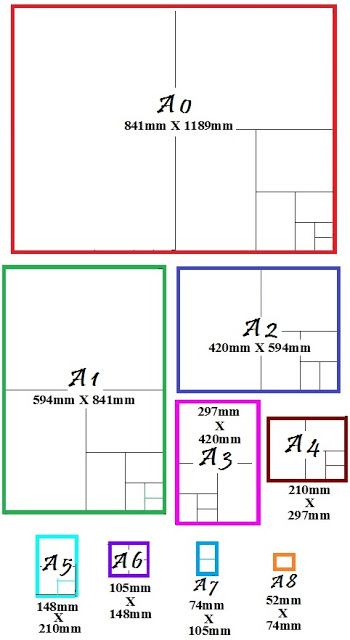
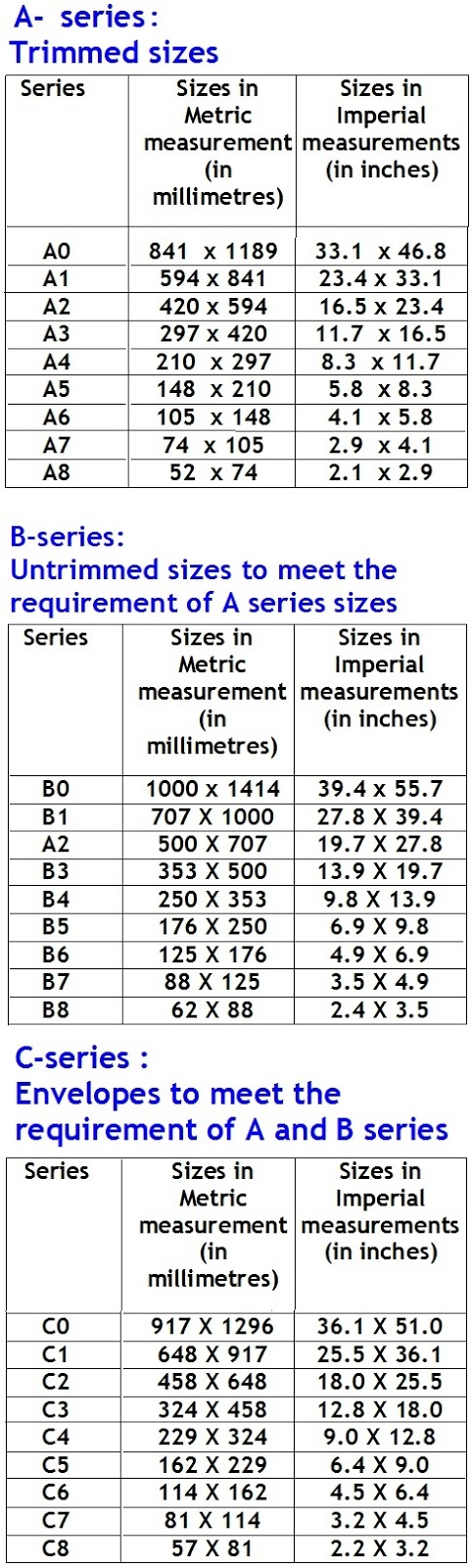
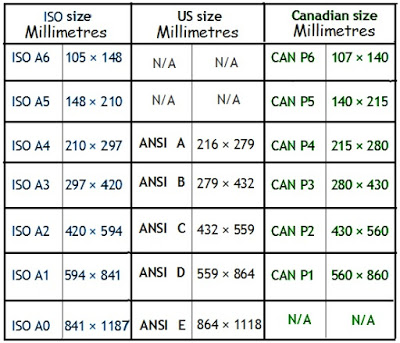
used in certain countries (Imperial size)
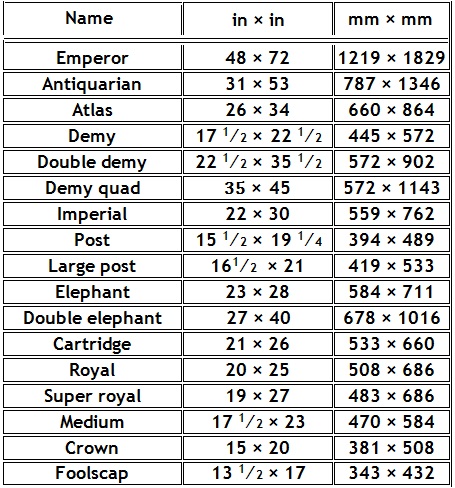
Recent Comments