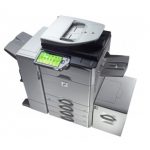
Guide to printing students -5
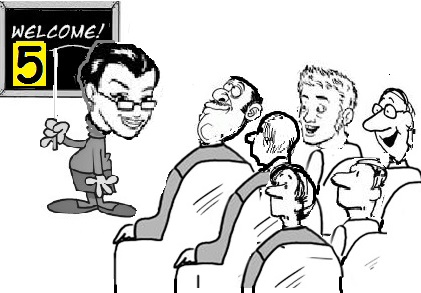
Guide to printing students
-Few objective Questions and answers-
Written by : N.R. Jayaraman
Pre note:-
The articles are meant to help the students gain knowledge and effectively compete in the interviews and nothing else. Please note that these are not to be published by anyone for commercial purpose without the written permission from the author since the theme and illustrative examples have been compiled exclusively by the author for the benefit of the student community. THIS WILL BE PERIODICALLY PUBLISHED.
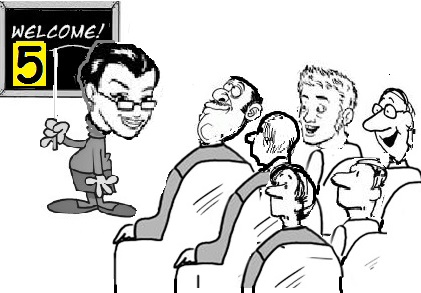
25) What type of ink is used in Intaglio printing process?
The pigmentation of Intaglio ink is very high. The varnish used have higher tackiness compared to other processes. The quality of the ink used in Intaglio is such that it remains slightly loosened (less viscous) while inking the plate due to heat generated in the ink fountain (heat apparatus fitted) and the plate cylinder inside which heating elements are fitted. The ink slowly dries on the substance on which it is printed by slight penetration cum oxidation cum polymerization process- one after the other taking place in quick succession to ensure that the relief effect of the ink required is not lost. Normally the standard Intaglio ink takes 2-3 clear days to dry and therefore in order to prevent set off on the backside of the printed substances, the same are interleaved with unpolished Kraft sheets like how the art papers are interleaved in Letterpress process of printing.
The pigmentation of Intaglio ink is very high. The varnish used have higher tackiness compared to other processes. The quality of the ink used in Intaglio is such that it remains slightly loosened (less viscous) while inking the plate due to heat generated in the ink fountain (heat apparatus fitted) and the plate cylinder inside which heating elements are fitted. The ink slowly dries on the substance on which it is printed by slight penetration cum oxidation cum polymerization process- one after the other taking place in quick succession to ensure that the relief effect of the ink required is not lost. Normally the standard Intaglio ink takes 2-3 clear days to dry and therefore in order to prevent set off on the backside of the printed substances, the same are interleaved with unpolished Kraft sheets like how the art papers are interleaved in Letterpress process of printing.
26) Why do you need heating elements in the Ink fountain and Plate cylinder on Intaglio machines?
The Ink used in Intaglio process is very stout and can not be even taken out by ink knives from the ink tins and are to be sucked by powerful ink sucking units fitted with heavy tubes that flows the ink into the ink duct.
The Ink used in Intaglio process is very stout and can not be even taken out by ink knives from the ink tins and are to be sucked by powerful ink sucking units fitted with heavy tubes that flows the ink into the ink duct.
In order to ensure that the ink filled in the ink duct gets agitated freely for uniform inking, the very stout ink need to be slightly loosened for a while till they are supplied to the special rollers that inks the plate cylinder. The engraved images in the plate cylinder has to also get filled with the loosened ink and then transfer the entire ink deposited in the pits on to the surface of the paper.
Once the ink is transferred on to the paper, it has to immediately start shedding its loosened form and to turn into its true (stout) form. Therefore in order to convert the original form of stout ink into temporary free flowing ink till they are transferred on to the paper, temporary heating arrangement is needed for purpose stated as above.
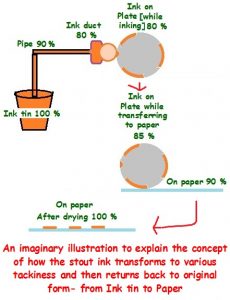
27) What type of ink is used in Gravure printing process?
The principle components of the ink used in Gravure printing is alcohol based. The materials like esters, ketone, glycols and water are used for the solvent part and cellulose, vinyl, acrylic and polymers and organic and mineral pigments are added for coloring and other properties. The selection of solvent is such that the pigments get dissolved in the binder and eventually after printing they evaporate during drying process. The ink used on this process should have higher colour value and being liquid, it has to stay inside the pits on the cylinder and also get transferred on to the paper surface in true tone and strength without loosing the strength or cause smudging on the edges.
The principle components of the ink used in Gravure printing is alcohol based. The materials like esters, ketone, glycols and water are used for the solvent part and cellulose, vinyl, acrylic and polymers and organic and mineral pigments are added for coloring and other properties. The selection of solvent is such that the pigments get dissolved in the binder and eventually after printing they evaporate during drying process. The ink used on this process should have higher colour value and being liquid, it has to stay inside the pits on the cylinder and also get transferred on to the paper surface in true tone and strength without loosing the strength or cause smudging on the edges.
28) What type of ink is used for Flexographic process of printing ?
In Flexography Printing Process too only liquid ink is used. The water based ink which is generally used in this process has to dry very fast as this process is meant to print on corrugated boxes, foils of various types especially aluminium foils of medicine packs, multi-wall sacks, paper sacks, plastic bags made up of various materials including food packaging etc. Therefore the ink has to dry by evaporation. The solvent (vehicle) is made up of typical alcohol, ethyl, propyl, or isopropyl etc to facilitate quick drying by evaporation on the substance in which they are printed and at the same time they should not evaporate and dry inside the ink duct. Typical resins or binders used in flexographic inks include acrylics, cellulose esters, nitrocellulose, poly amides, modified rosins, and ketone etc. The water based ink has pigments or the dyes in colloidal suspension and the composition of the ink is somewhere in the range of 60% to 65 % water, other solvents 15 % to 20% as vehicle (resin) and 10 % to 15% colorant with remaining being suitable additives.
In Flexography Printing Process too only liquid ink is used. The water based ink which is generally used in this process has to dry very fast as this process is meant to print on corrugated boxes, foils of various types especially aluminium foils of medicine packs, multi-wall sacks, paper sacks, plastic bags made up of various materials including food packaging etc. Therefore the ink has to dry by evaporation. The solvent (vehicle) is made up of typical alcohol, ethyl, propyl, or isopropyl etc to facilitate quick drying by evaporation on the substance in which they are printed and at the same time they should not evaporate and dry inside the ink duct. Typical resins or binders used in flexographic inks include acrylics, cellulose esters, nitrocellulose, poly amides, modified rosins, and ketone etc. The water based ink has pigments or the dyes in colloidal suspension and the composition of the ink is somewhere in the range of 60% to 65 % water, other solvents 15 % to 20% as vehicle (resin) and 10 % to 15% colorant with remaining being suitable additives.
29) What type of ink is used for Silkscreen process of printing process?
The composition of the inks of Silkscreen has higher Pigmentation (say 30 % as technologists say) rest being binders, solvents and additives. Screen process printing requires paste form of inks that are thicker, but are able to pass through the small holes in the screen to leave sharp prints on the substance. Binders are typically resins and form part of the vehicle in the ink. The binders remain on the substrate or surface along with the colorant (pigments) and therefore the binder added to screen printing ink must be compatible with the surface on which it is printed. The solvents used should also not be highly volatile, as early evaporation would cause the remaining ink dry on the screen.
The composition of the inks of Silkscreen has higher Pigmentation (say 30 % as technologists say) rest being binders, solvents and additives. Screen process printing requires paste form of inks that are thicker, but are able to pass through the small holes in the screen to leave sharp prints on the substance. Binders are typically resins and form part of the vehicle in the ink. The binders remain on the substrate or surface along with the colorant (pigments) and therefore the binder added to screen printing ink must be compatible with the surface on which it is printed. The solvents used should also not be highly volatile, as early evaporation would cause the remaining ink dry on the screen.
30) What is meant by Viscosity of the ink ?
This describes the degree of fluidity of a liquid ink as far as printing is concerned. Viscose means the thickness. A high viscose ink means the ink is thicker and does not freely flow. Each variety of ink is made in different viscosity to suit the process and the substance or Paper for which it is intended. The Ink meant for Letterpress printing may not be suitable to Offset, or Intaglio printing and vice verso for this reason.
This describes the degree of fluidity of a liquid ink as far as printing is concerned. Viscose means the thickness. A high viscose ink means the ink is thicker and does not freely flow. Each variety of ink is made in different viscosity to suit the process and the substance or Paper for which it is intended. The Ink meant for Letterpress printing may not be suitable to Offset, or Intaglio printing and vice verso for this reason.
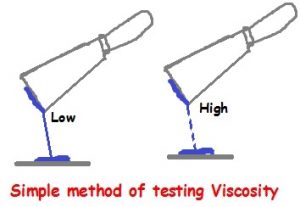
31) How important is Tack in ink ?
The term tack refers to the amount of stickiness of the printing ink and should not be confused with viscosity. Printing inks are required to have internal cohesion with pigments and other particles present so as to sit firmly on the surface on which they are printed. If the tack is higher, then it will pull the fibers from the surface of the paper. Higher tack ink can also cause picking problem. Increased or insufficient ink tack can influence the reproduction of solids, sharp lines and dot gain. However in respect of Offset printing, if the tack is not slightly higher then it can cause emulsification in the fountain solution. Every ink contains vehicles, pigments and solvents in balanced proportions and their proportion determines the tack properties. The tack is an important factor for the transportation of the ink between rollers and for drying properties.
The term tack refers to the amount of stickiness of the printing ink and should not be confused with viscosity. Printing inks are required to have internal cohesion with pigments and other particles present so as to sit firmly on the surface on which they are printed. If the tack is higher, then it will pull the fibers from the surface of the paper. Higher tack ink can also cause picking problem. Increased or insufficient ink tack can influence the reproduction of solids, sharp lines and dot gain. However in respect of Offset printing, if the tack is not slightly higher then it can cause emulsification in the fountain solution. Every ink contains vehicles, pigments and solvents in balanced proportions and their proportion determines the tack properties. The tack is an important factor for the transportation of the ink between rollers and for drying properties.
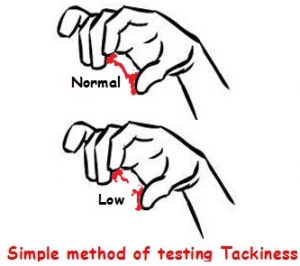
continued…………. 6
Recent Comments