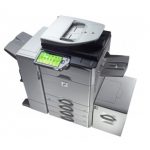
Alphabet – M /2
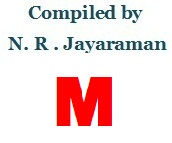
10. Mark-Up copy: The instructions usually written on the manuscript ( model version of each section of the printed material ) to guide type setting process and the compositor is called ‘mark up copy’. These instructions would indicate the type face, point size, weight of paper to be used, headings, captions etc.
Also the proof read copy is called mark up copy. They too contain several instructions and corrections in brief. The methods and techniques for marking copy are evolving rapidly. The illustration below will show proof readers’ marks are used in hard-copy editing which is submitted as mark up copy.
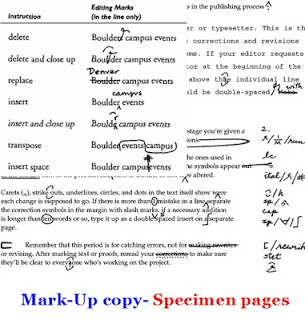
11. Matte Finish : It is a term used both in photographic and Printing processes to indicate the surface finish of the paper.
Unlike coated stocks which give glossy effect, the matte finish printing paper does not strain the eyes and show the image in sober color. The absence of glow help make the print viewable from any angle without straining the eyes. This also suits best for ink jet printing.
The matt finish photographic papers (Bromide papers to take photo prints from films) can give portraits a softer appearance even though the same print on glossy paper will appear vibrant. But for process work, prints on glossy paper is discourages as the camera lights falling on the glossy paper can cause glare during exposure of the films.
In the case of films, the matt finish refers to slight rough surface on the emulsion side of the film. The matt films will be ideal to work with Photo polymer plates which have smooth surface. The photo polymer plates work well with matt base films as they give better contact between the film and the plate surface and does not slip due to smooth surface of the plate and also the chances of static electricity occurring on account of two smooth surfaces – smooth base film and smooth surface plate- are minimized.
12. Mechanical Binding: The technique of binding the books and note books which are pre-trimmed to correct size. This process does not require any adhesives, stitching or sewing and uses plastic material or thin metal called spirals to keep the loose leaves bound. They are inserted in the holes punched on the back portion of the books and rotated to hold from end to end and therefore this mechanical processed binding is called mechanical binding. Example of such binding includes Comb binding or spiral binding. The dairies, table top calendars, desk note pads, thesis papers, research papers, annual reports, budget reports and other jobs are done by this technique -mechanical binding.
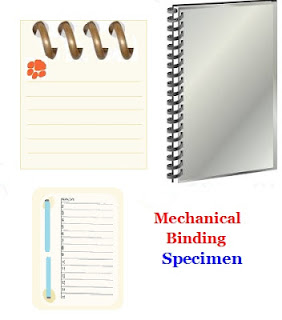
13. Mechanical pulp : In the paper making mills both wood pulp and cotton comber pulps are used for manufacturing the paper. While cotton comber pulp is used for very good quality and smooth paper, the wood pulp paper is used in newsprint, as well as papers used in telephone directories, catalogs, cheap priced magazines, paper towels and tissues etc. Since the wooden blogs are mechanically converted (crushed) into fibers it is called mechanical pulp.
In the paper making process the cotton wool is chemically treated to make pulp while in the case of wood pulp, the wooden chips are ground against stone grinders (special machine) which first chip them into fibers and then with the crushed wooden fibers the pulp is made. The process of mechanical pulping involves forcing logs against a revolving stone which grind the logs into pulp by abrasive action. The stone is sprayed with water to remove fibers from the pulp stone as well as to prevent the fiber getting damage due to friction-generated heat. The advantage of mechanical pulp is that it produces high pulp yield thus reducing the cost. It is stated that the wooden fiber yield is around 90-95% compared to the cotton comber fiber pulping which yields around 75-80 % good quality (long) fibers only. The mechanical pulp paper has more ink absorbency, but at the same time the paper strength will be less (ex : News Papers) compared to other good quality paper used in magazines. Since the wooden logs contain natural organic compound known as lignin which is sensitive to light, the paper shade turns to brownish or discolors in few days when exposed to light. This is another disadvantage of using mechanical wood pulp.
14. Mechanical Tint: The artists while making art or designs, produce special effects by drawing lines and dots of different sizes and thicknesses. Some times the special effects are also given in some portions with different design elements. But such an exercise takes much time. In order to hasten the process, the mechanical tint design papers have been introduced. The different shades and designed patterned sheets are made available by different manufacturers.
The mechanical tint design papers are something similar to the adhesive papers used in labels, but carry reproducible printed design elements on it. The basic difference between the adhesive labels and the mechanical tinted papers will be the paper thickness and transparency. The mechanical tinted paper will be very thin so that it can easily merge with the art work without showing relief on their edges.
Sheets of mechanical tints representing a full range of values of dots, screen ruling, lines, waves, and other designs available as mechanical tint paper will be cut up and directly added to drawings. Such mechanical papers with color elements are also available to speed up production artists work in color. Wherever needed, the design elements will be cut to the design shape and pasted into the art work directly. The mechanical designs are mostly used on art works that combine photographic halftones with graphic design and are of simple nature.
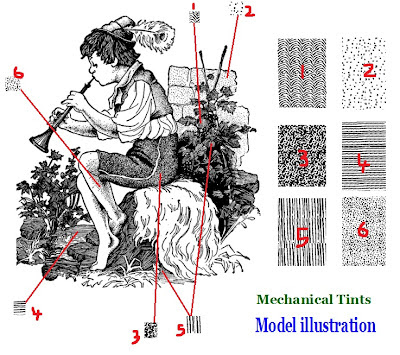
15. Metallic Ink : Metallic ink contain powdered metal like pigments that simulate metal. It is those particles that makes the images shine. Metallic inks not only give glossy look to the print but also enhances the quality. The metallic inks are also used in inkjet to print on garments as a spot color, which however fades away after few wash . Therefore the metallic inks can not be mixed with other colors as they will affect washability. Generally the metallic inks are not used on high web printing presses as the ink is hard and does not have smooth flow and the the metallic particles need to be kept on mixing constantly to mix up well with the base ink. Even then metallic inks to print on Offset and Letterpress machines are available in the industry.
a. Manufacturer and suppliers names, addresses, and emergency phone numbers
b. Physical data of the product
c. Explosion or fire hazard data
d. Hazardous ingredients in the product
e. Toxicological properties
f. First aid measures in case of accidents with the said product etc
Recent Comments