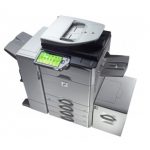
Guide to Students in Printing – 27
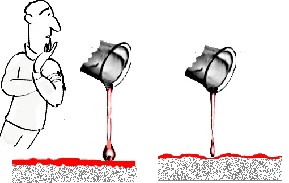
-Few objective Questions and answers-
Written by : N.R. Jayaraman
112) What factors influence production of a good plate?
The following major factors influence the production of a good plate:-
- The plate grain
- Thickness of coating
- The colloid-Bichromate ratio
- The whirler speed
- The RH, PH of the coating and Temperature
- Age of the coating solution
- Time period of the coated plate before exposure
113) Explain the above factors in brief.
(a) The plate grain is very important in holding the images and giving wettability to the plate during press run. If the grain is too fine, the coating will become thin and developer and subsequent etching chemicals can intrude into the coating and lessen water affinity of the non image areas thus leading to scumming during printing. At the same time if the plate is too coarse, the peaks of the grains (gap between the lower and top surface of the pit) may hold less coating while the pits will have more coated material (thicken the coating) which will harden and stick to the grains thus becoming difficult to clean. Thus it will also cause scumming tendency of the printing plate. Therefore the graining should be consistent with medium (neither too fine, nor coarse) grain to be maintained from plate to plate to suit the standardized coating solution prepared in-house.
(b) The coating solution plays a vital role in the formation of the image. If the viscosity of the coating solution which determines the flow of the solution is more, then the coating on the plate will not be even. If it is too thin, the image adherence power will be less. Therefore the viscosity of the coating solution must match the grains of the plate. The plate maker generally uses a Viscometer to test the viscosity of the solution to match the grain after he standardizes the grain on the plate required along with the composition and ratio of the material in the coating solution.
(c) At the same time the whirler speed also determines the thickness of the coating. If the speed is more, the coating becomes thinner and if the speed is too less, the coating remains thick. See the illustration below to understand how the whirler speed can affect the coating.
(d) The ratio of Bichromate vs the colloids (Gum or Albumen) affects the viscosity and sensitivity of the coating solution. While the viscosity governs the thickness of the coating as the solution will have to evenly and freely spread on the plate during coating, the sensitivity determines the exposure and the hardening effect of the coating. See the illustration below to understand the how the plate gets affected due to variations in the Bichromate ratio and sensitivity of the solution.
(e) The temperature and humidity too cause variation in the sensitivity of the solution which in turn influence the coating thickness. If the temperature increases, then the coating becomes thinner.
(f) Similarly variation of the RH (moisture content in air) also affect the coating thickness and drying time on whirler. When moisture content increases it thins down the coating solution and also takes more time to dry and more time to dry means, needing more rotations in the whirler to dry the moist coating.
(g) The plate after coating and drying should not be allowed to wait for longer time for exposure as longer time after coating will keep the continuing action of drying which will in turn keep hardening the coating which will affect the image on the plate.
(h) The coating solution should also be not made in bulk or kept for longer period (days) as the solution will keep losing its sensitivity even when it is kept in dark room shelf.
(i) In short when the RH, Temperature, Whirler speed, and Bichromate ratio in coating is on the higher side, then the coating becomes not only thinner but also more sensitive.
Recent Comments