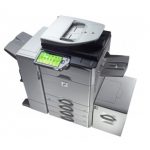
Guide to Students in Printing – 28
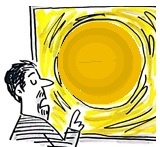
-Few objective Questions and answers-
Written by : N.R. Jayaraman
112) What troubles one normally encounter in Surface plate making process?
- Non-uniform Plate coating due to thick coating solution. The thick coating can be due to improper ratio of ingredients in the coating solution or solid particles in solution due to improper mixing of the ingredients.
- Weak image and scumming on plate in non image areas. The scumming is due to thick coating which slightly hardens on account of the heat generated in the exposure unit, dark or continuing reactions and may have become hard to clean.
- Thinner Coating leading to scumming on non image areas. The thinner coating could be due to thin 9less viscosity) coating solution, higher whirler speed, increase in temperature or higher humidity etc. Also the thinner coating could be due to improper ratio of the chemicals including water used in the solution.
- Difficulties in developing after exposure either due to Continuing reaction or Dark reaction. Water too cold and not able to wipe out the unhardened coating on non image areas. Low density of black paper which may have been used to mask the non-printing areas. The black paper may not have been dark enough (opacity) to stop the light and instead allowed the light to pass through its surface partially hardening the non-image areas. Also the black areas in the film negative may not be dark enough (it is called density) to stop the light from passing through. All these factors lead to improper development of the plate.
- Plate developing scum due to improper gumming after processing. Improper gumming lead to partial oxidation of the non-image areas which lessens the water affinity.
- Weak image due to improper adherence of the coating solution over the plate whose grain may have been coarse.
113) What is known as Continuing reaction and its impact in plate making process ?
Once the chemical reaction of hardening process begins on the coated plate after exposure to UV light, the hardening act of the coating continues in invisible form unmindful of the fact that the plate is kept completely in dark away from being exposed to light. This invisible continuing reaction of hardening on the exposed plate is called Continuing reaction. Therefore the plate should be developed immediately after exposure to UV light without allowing much time to lapse, lest the continuing reaction will produce scum on the plate. The continuing reaction is not limited to Surface plate but also applicable to Deep etch plates.
114) What is known as Dark reaction and its impact in plate making process ?
Once the coating solution is mixed with sensitizer like Ammonium Bichromate, the chemical reaction begins in the coating solution which lowers the sensitivity even though the coating solution may have been kept in absolute dark place free from other lights. Once the sensitivity begins to go down, the internal hardening process gets hastened leading to improper development. The silent chemical reaction which takes place in the coating solution even when the same is kept in dark is called Dark reaction. The Dark reaction does not begin as long as the sensitizer is not mixed in the coating solution.
This is the reason why in the process room, the coating solution is prepared on need base basis by mixing A and B solutions or basic ingredients like Albumen or Casein plus the sensitizer if it is prepared in-house, after sufficient no of plates to be prepared is worked out. Generally the coating solution is prepared only few minutes before processing starts whether ready to use coating solution is used or as prepared in house. The suppliers supply the coating solution as A and B separately with A as the base solution and B the sensitizer. Therefore the coating solution should not be kept for too long a period after the sensitizer is mixed, lest the Dark reaction will produce scum on the plate. The Dark reaction is not limited to Surface plate but also applicable to Deep etch plates.
115) What troubles one normally encounter in Deep etch plate process?
- Non-uniform Plate coating. The thick coating solution can be due to improper ratio of ingredients mixed in the coating solution and solid particles found due to improper mixing of the ingredients.
- Weak image and scumming on plate in non image areas. The scumming is due to the thick coating which slightly hardens on account of the heat generated in the exposure unit. Also due to improper adherence of the coating solution over the plate whose grain may have been coarse or the developer may not have developed the areas properly for etching due to improper ratio of chemicals in the developing solution or improper ratio of chemicals in the etching solution makes the etching solution weaker and unable to etch the images properly.
- Hard to develop and etch the image after exposure due to Dark reaction taking place in the sensitizer solution after mixing which may have begun to harden partially even though they were kept in dark. Also the images on the positives may not have been dark enough (it is called density) to stop the light intruding in and instead partially allowed the light to pass through thus hardening the image areas. These factors makes it difficult to develop or etch the plate properly.
- Scumming on plate is also due to cold water unable to wipe out the coating in the non-image areas after developing and etching. Also improper gumming after processing the plates leading to partial oxidation of the non-image areas which lessens the water affinity. This could also arise due to thinner coating which caused partial hardening of the non-image areas.
Recent Comments