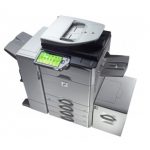
Alphabet- F /2
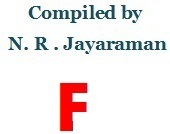

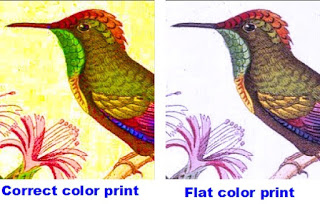
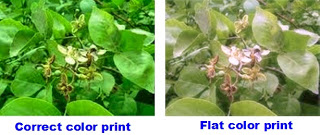
13. Flexography : One of the printing process in which rubber or photo polymer plastic plates with relief images are used for printing. This process suits best for carton printing, printing on medicine packs-both paper and metallic foils, gift wrappers, wrapper foils wall covering, magazines, newspaper inserts, paperback books, telephone directories, and business forms etc . Printing on food packaging is an important area where flexographic printing is successfully employed.
Earlier this process of printing was known as aniline printing because flexographic inks contained aniline dyes. Basically this process of printing need evaporating solvent based inks. The ability of flexography to print on a variety of substrates allows the process to be used for a wide range of printed substrate including plastic, metallic films, cellophane, and on paper. As the name suggests flexography is a printing process which uses flexible relief plate that can be easily clamped to a printing cylinder and therefore best suited for high speed rotary printing presses. It is basically an updated version of letterpress.
This process will be ideal for printing on non porous substance; hence the inks that dry by evaporation will best suit this. This process ideally suits for printing large areas of solid color provided high density of the said color will not be the need. Flexography continues to be one of the fastest growing print processes and is no longer reserved just for printing specialty items.
Flexographic printing inks are primarily formulated to remain compatible with the substrates used in the process. Each formulation component individually fulfills a special function and the proportion and composition will vary according to the substrate used. There are few types of inks that are used in flexographic printing process. Basically they are Quick evaporating solvent-based Inks, Water-based Inks and Ultraviolet curable Inks. The ink is supplied to the plates by a roller called anilox roller which plays an important roll in this process. The anilox roller a hard cylinder shaped roller constructed of a steel or aluminum with ceramic coating that has thousands of very fine cells. The number of cells per inch determines the ink flow that can be accomplished. Cell counts in anilox rolls range from about 150 per inch to 500 per inch. As the cell count increases, the amount of ink delivered by each cell decreases thereby allowing delivery of much smaller portions of ink to much smaller areas of the substrate.
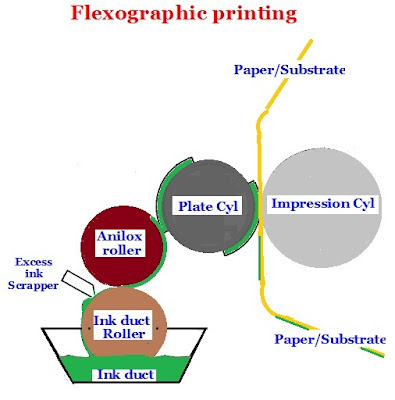
14. Form Roller: The entire set of rollers that come in direct contact with the printing plate on the machine is called the form roller. In all printing processes including wet Offset printing, the rollers that feed ink to the plate is called form rollers. In wet Offset printing, in addition to the inking form rollers, a set of felt covered rollers which dampens the plates are also fitted. They are also called dampening form rollers .
The form rollers in the inking unit takes the thin film of ink from a series of intermediate rollers that draw the ink from the ink fountain, rotate along with the speed of the machine to grind them before supplying a uniform layer of ink to the form rollers. The form rollers do not directly take the ink from the ink fountain and draw the ink layer from the intermediate rollers. Similarly the form rollers in the dampening unit of the wet offset printing gets dampened by the set of intermediate dampening rollers which draw the water from the dampening unit fountain solution and then supply water to the form rollers which then dampens the plate to resist the ink in the non printing areas.
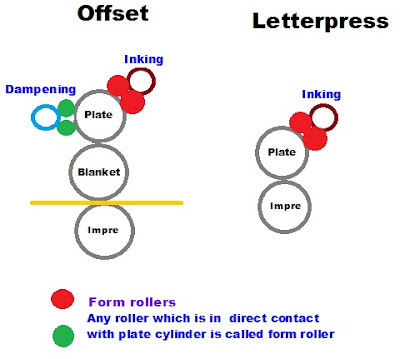
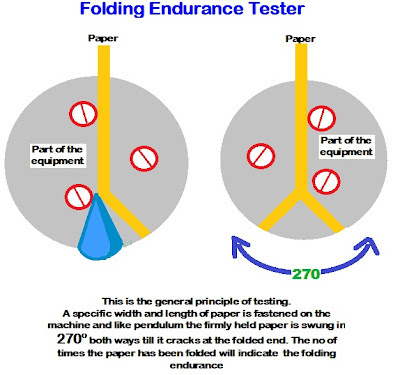
16. Fountain : A Tray or a Trough or a Container that holds fluids such as ink, varnish or water in a printing machine is called Ink fountain, water fountain, varnish fountain etc, The fountain is also called a duct. Every printing machine irrespective of the process used will have a duct containing some fluid material required for the machine as stated above. In short the duct is the main supply base of such fluid material. While machines like Letterpress, Dry Offset, Intaglio, Gravure, Flexography have ink ducts, the wet Offset additionally has a water duct that supply water to the dampening rollers.
17. Fountain Solution : Mixture of water and chemicals that aid effective dampening of the printing plate to prevent ink from adhering to the non image area. Such water based chemicals will be called dampener solution and such arrangement is found only in the Wet Offset printing process. In the Intaglio printing process too some solution similar to fountain solution like caustic soda-castor oil combination is provided in a tank from which a wiping cylinder in contact with the plate cylinder clean the non image areas.
18. Flying and Misting : A spray or mist of ink is visible in the air around the printing machine which eventually settles, covering the machine with a thin film of ink. This may be the result of defective ink, the high speed of the machine in general and emulsified ink in wet offset printing.
18a. Fluff or debris: Fluff or debris is a printing defect caused by lint and dust particles partially embedded on the paper surface getting released and struck on the surface of the plate cylinder. If the partially embedded particles are not removed from the surface of the paper, they may get released along with the inked image from the blanket cylinder surface which in turn get struck to the surface of the plate cylinder. Those particles on the plate cylinder will not accept the ink from the inking roller and cause voids on the successive prints. They are called fluff or debris or sometimes as Lint. Use of powerful anti static rod fitted suction unit will help in reducing this problem.
Recent Comments