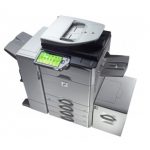
How is the production capacity calculated ?
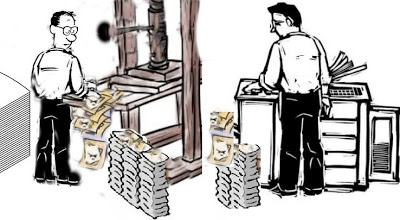
How is the production
capacity calculated ?
(Written by : N.R. Jayaraman)
What will be the ideal production capacity of a machine printing 40 ups per sheet ? How is it determined ?
Before we proceed further, be aware that the norms can be fixed only :-
- For those presses where the same design is printed in millions throughout the year.
- The press which is engaged in the printing the same design on long term contract through the year.
- Even if there is change in the design it will be effected only after several days of working with the same set of plates/ blocks.
- Those engaged in the printing of Bank notes, Currencies, Detergent wrappers, fast selling several Consumer product labels and wrappers in several thousands , Raffle tickets etc.
- The basic requirement for fixing the norms are that the plant should have regular long run print order and not those printing short run copies and irregular print orders.
- The norms can also be not fixed for those which are printing multi colour work with design change every day.
The following factors will determine the production capacity.
- Rated speed of the machine as suggested by the manufacturer
- Working hours per Shift – 8 hours or more
- Whether over lapping shift is in force
- No of shifts per day
- No of working days per week
- No of days the unit work per year
- No of declared holidays per annum
The data shown under are only illustrative for educative purpose to show the methodology and figures not actual as every unit will have their working pattern. Therefore the working pattern of the press will have to be taken into account before calculating the actual figures. Let us presume the following:-
- Machine speed as suggested by the manufacturer : 10000 sheets per hour
- Working hours per Shift : 8 hour per shift
- Whether over lapping working is in force : No
- No of shifts per day : Two
- No of workmen per machine ( This will be necessary to distribute the work for faster moment of work )
- No of working days per week : Six with weekly Off on Sundays
- No of declared holidays per annum excluding holidays : 14
- No of days the unit work per year :
- Declared : 14
- Sundays : 52
- Absenteeism caused non working 15 days per annum 365 – (14+52) -15 = 284
A) The following factors will be considered as non productive hours :
(1)Make ready before actual production that includes Fixing plates, loading of paper, color setting, registration etc say about one hour (60 minutes) max. If the job is of regular run which is continued for few days without changing the plates or colors, then initial setting time which includes ink charging, loading of paper and other settings etc is 30 minutes
(1)Make ready before actual production that includes Fixing plates, loading of paper, color setting, registration etc say about one hour (60 minutes) max. If the job is of regular run which is continued for few days without changing the plates or colors, then initial setting time which includes ink charging, loading of paper and other settings etc is 30 minutes
(2) Machine to stop before Lunch, say 10 minutes .
(3) Restart time after lunch say 10 minutes
(4) Machine to stop before next shift working say 15 minutes .
All these factors thus takes away on an average one hour per shift for regularly run work from the shift hours.
- In view of the above the non productive hours per shift becomes approximately 1 hour in 8 hour shift. Therefore we will have 7 hours left for production activity.
B) Even though the rated speed of the machine is given as 10,000 sheets per hour by the manufacturers they are only theoretical figures and it will not be possible to instantly start printing 10,000 sheets per hour the moment you switch on the feeder. Every time the machine stops and restarts for some reason or the other, the speed of the machine comes down before picking up the full speed on restart and therefore the average speed will be 75 % of the rated capacity only. accounting to an average of 7500 sheets per hour on an average .
During the process of printing due to several technical problem s connected to ink, paper , dust, and colour adjustments one can expect the machine to stop at least once every hour especially on presses where blanket cleaning at certain intervals will be inevitable. Every time when this happens minimum 8- 10 minutes loss will be there before restarting the machine.
- Therefore with minimum 8 times stoppage and restart of the machine per shift the loss of productive hours will further be accounted to one to 1½ hour on an average.
Therefore we will be left with the following no of hours for production :
- 7 (See ‘A’ above) minus further 1½ hour on an average (‘B’ above) leaving 5 hours and 30 minutes for production activity.
(C) Again for unforeseen activities like blanket change, plate change, packing adjustment, machine break down repairs, week end cleanings, week beginning make ready time etc another 10 % down time allowance is added .
Therefore considering the above we will be left with the following no of hours for production:
Therefore considering the above we will be left with the following no of hours for production:
- 7 hours (See ‘A’ above) minus further 1½ hour on an average (‘B’ above) minus 10 % ( 45 to 50 minutes) which will work out as 4½ hours for actual production .
Therefore in 4½ hours the machine can surely produce the following quantity of production:
- 7500 sheets per hour X 4½ hours = 33750 sheets or 33750 ÷ 500 sheets = 67.5 reams in ideal condition . The 67.5 reams with 40 up images will be equivalent to 1.35 million (67.5 Reams X 500 sheets X 40 Ups = 1350000 ups or 1.35 million) per shift.
Taking the above figure as targeted production the annual capacity can be assumed as below:
- 33750 sheets per day per shift X 2 shifts X 40 ups x 284 days of working = 766 millions rounded to 750 million on the lower scale and to 800 million on an upper scale.
Recent Comments