From hand composing to Photo composing
(Written by: N.R. Jayaraman)
It will be interesting to read the origin of typesetting which has now culminated into Photo composing and Digital printing. Around 600 to 700 years back there were no typefaces to print. The knowledge was spread by word of mouth and by the end of the century some documents or leaflets were brought out with hand written scripts.
During Roman Empire some of the artists practiced the art of Calligraphic writing to put on record what they learnt. During the same period, preaching of Bible began to spread all around Europe by word of mouth and therefore the production of manuscripts in some formats became the need of hour.
Cursive (running lines of writing) was a form of handwriting or scripting practiced during the ancient Roman period as well as in the Mid ages. The alphabets or letters scribed during old Roman period were known as ‘Majuscule cursive*’ and ‘Capitalis cursive’ (*meaning big letters, even to the extent of one inch in height) scripts. They were also called Uncial* lettering (*an inch in size letters square in shape) by some group in Europe and practiced for writing letters, business accounts of traders, and in schools to teach Latin language. The first of the Bible was in Latin language. Besides uncial letter scripts were also used for issuing commands of Emperors.
Later some years, unlike in Rome, Ireland artists developed better formation of the scripts called ‘Celtic letters’ which were smaller in size and round in appearance (Typefaces) instead of square shaped ones. Remember all the documents during the initial Roman period continued to be hand written till the printing process using typeface or letter fonts was invented.
However the credit for the introduction of better format for typefaces to publish documents goes to some of the Roman Emperors, particularly to ‘Charles the great’ or ‘Charles-I’ as he was known, in whose period the practice of using standardized lettering was advocated. A more formal style of writing based on square Roman letters, but cursive in style was practiced. Charles-I also known as ‘Charlemagne’ was an undisputed leader of Frankish Kingdom and united most of Western Europe under Roman Empire. He died in Germany. He was actually instrumental in standardizing the style of scripts,namely calligraphic for documentation of texts for future references.
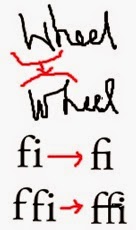
The artists during his period realized that the Old Roman cursive was very difficult to read particularly the ‘Latin’ script which had too many ligatures* (*two or more letters joined to show as single letter), while some letters remained even unrecognizable. In the first three centuries AD the Roman Cursive scripts, which looked more like capital letters (combination of capital and lower letters) were extensively used and that was the cause for unrecognizable appearance.
Cursive handwriting
Page from the Lorsch Gospels of Charlemagne’s reign
(Picture courtesy:- http://en.wikipedia.org/wiki/Charlemagne)
Next to Old Roman cursive script came the New Roman cursive called ‘Minuscule cursive’ that replaced ‘Majuscule cursive’ script. This was widely practiced in the 3rd to 7th century. The major advantage was that the letters were more recognizable, letters proportionate to each other rather than varying wildly in size. The different styles of handwritten script used for the production of documents continued to surface though the process of writing entire book by hand which of course was labor-intensive and needed assistance of well trained artists and script writers till Gutenberg introduced the movable types in the 14th century. Gutenberg reproduced ‘Gutenberg Bible’ or the ‘Mainz Bible’ in 17th century with around five million characters, each of which had to be cast in metal, and each letter picked up by hand from a box, assembled into lines and made up into pages for printing.
Johann Gutenberg
Johann Gutenberg used one of the textur typefaces for his famous Gutenberg Bible, possibly the first book ever printed with movable type. It is said that 300 different pieces of types were used to print the Bible in the year 1455. Black letter script called Schwabacher, more rounded in shape soon became usual printable typeface, but it was replaced by another script called Fraktur in the early 17th century.
In the 13th century, engraved images on wood were inked and prints taken. This paved the way for the development of wooden types for printing. However it required skilled craftsmen to carve out entire pages of text into wooden blocks. Once the text was carved, the space around the letters had to be whittled away so that only the text in relief would touch the paper. During 15th century some books were reproduced with wood cut blocks which however did not have removable typefaces. The scripts to be printed were engraved on wood and were printed by placing the paper over the wooden blocks and rubbing the back of the paper with slight pressure with a cloth or roller like object. Corrections could not be carried out once the wooden block was chiseled.
Chinese printed document
One school of thought say that woodblock printing developed in Asia several centuries before printing with typefaces surfaced in Europe. According to them the Chinese were the first to print solid text material on fabric and paper and Europeans recast the Chinese version of printing the images on cloth into the printing images on paper using woodcut blocks. Their argument is based on the belief that the Buddhist texts printed on paper in China during 6th and 7th century were excavated between 1966-74 in some parts of China and Korea. Further, in 10th century wooden block printed Buddhist Canon Triptika running to 1,30,000 pages have also been discovered. In support of their claim it is pertinent to mention here that Chinese were the first to invent the Paper making process in the 6th century and therefore such an argument can not be brushed aside. It is also now established that sometime in mid 14th century similar to Chinese process of printing substantial amounts of texts were printed in Europe using wooden blocks after movable typefaces came into being as invented by Gutenberg.
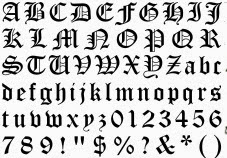
Black letters
Gutenberg used the script called Black letters, which were thick scripts. In the next few years use of Black Letter (sometimes called Old English or Gothic) spread to many parts in Germany. Black Letter script was used by Gutenberg for the movable type which he invented. From this point of time came the typographic printing process.
There is however a different claim that prior to the invention of movable typefaces by Johannes Gutenberg in 14th century, Chinese had already invented some form of movable typefaces in baked clay sometime in 11th century while in 13th century Koreans invented the movable metal types. But they were not widely known and may have confined to smaller areas in China or Korea. The authentic historical data is however not available.
After the discovery of movable types by Gutenberg, the next few years saw wider use of hand composing process using movable typefaces for printing jobs. When Johannes Gutenberg perfected the technology of movable type in mid 14th century, it was realized that letters of the alphabet, numerals, and other marks made on durable metal could be assembled into a pages of text, then disassembled and re-used again to compose new pages of text like recycling process. The types were composed by hand into several lines of text and tightly bound together to make up a page called a forme. The forme was tightened in a metallic frame and mounted on the hand operated printing machine, inked, and an impression taken on paper.
The movable types by Gutenberg lacked in an important aspect. The letters were not of uniform size, uniform height and character were also not proportional to each other. They were more or less like hand written script types. At the same time attempts were also made to standardize the typefaces which can be universally accepted. Reason being slight non uniform height of movable types manufactured then needed under packing of individual letters to keep them in uniform height to touch the paper surface to produce uniform print.
Hand composing
During the end of 14th century one of the artists from France who was actively associated with Gutenberg namely Nicolas Jenson succeeded in standardizing the typefaces both in design and other aspects. When Gutenberg introduced single letters, the individual letters were alphabetically placed in a single tray containing partitioned boxes of uniform size. The tray was kept on a slanted table, individual letters taken from the boxes and assembled into words and positioned in a frame with supports to ensure that the composed lines did not fall and after completion of the typesetting. The typeset text was tightly locked from all sides with wood and other metal. The locking keys were much later generated tools and were not available to lock up the matter.
As the time taken and effort required for composing the matter was too long, further experiments based on practical difficulties led to the use of two trays instead of one with several partitioned boxes to carry lower case and capital letters separately. This was further improved upon with different sized boxes in the same tray to accommodate more and lesser quantity of typefaces. Bigger box was assigned for keeping letters that were more in use in words (like a,e,i,o & u) and smaller boxes for the letters which was occasionally used (like z,q,x etc) in the formation of words that formed a complete text. For a very longer period this manual composing technique continued to be used by the printers.
The credit for the establishment of a metal type foundry in 15th century to produce fonts for the printers goes to a Frenchman named Claude Garamont, who specialized in type design and punch-cutting. He produced superior types with several characteristics. In a short span of time the fonts produced by him became popular.
Hand typesetting (Composing), and correcting by hand remained an elaborate and time consuming process as every word had to be laboriously set from individual types and after printing each metal letter had to be put back into their respective boxes so that they can be reused again for composing other text material.
From the time Gutenberg invented movable typefaces, the trend of hand composing continued in the next four to five hundred years and remained largely unchanged. In 19th century, in order to ease the strenuous task of hand composing, mechanical typesetting machines called Linotype and Ludlow type were introduced. In the year 1884-86 first of the kind mechanical typesetting machine called Linotype was introduced by Ottmar Mergenthaler. The Linotype machine got its name as Linotype as it cast composed matter as lines of slugs. Ottmar Mergenthaler was born citizen of the Kingdom of Württemberg. Though by birth he was citizen of the Germany, at the time when he invented Linotype, he was a citizen of the United States of America. Therefore the credit for the invention went to American printers.
Linotype mechanical typesetter
Mechanical typesetting removed hardship involved in setting the type by hand by picking individual letters. Fitted with a keyboard, the Linotype machine operator enters text on a 90-character keyboard. The machine assembles a line of letters called matrices, which are moulded text that fall in a chamber in series of lines. Each of the assembled lines are then cast by molten metal as a single piece called a slug that carry the text material in the form of cast typefaces. The matrices are then returned to the type magazine from where they came for reuse again and again. This machine allowed much faster typesetting than hand composition.
Matrices with engraved
typefaces and slugs cast
The Lino typing revolutionized the typesetting especially for the production of newspaper which needed faster composing within short span of time. However Linotype machine too had limitation particularly in respect of font size. The machine could compose only specific size of font assigned to the machine and therefore the heading and subheadings had to be hand composed and inserted along with the Lino composed slug to form the pages. Also the individual spelling mistakes if any in words after the slugs were cast could not be carried out at a later stage and the entire slug having even a small spelling mistake had to be recast and replaced. This necessitated the perfect proof reading line by line once the matter is composed, but before casting them as slugs.
However the machine had several other advantages. It not only eliminated the laborious task of setting the types by hand but also eliminated the process of manually distributing back the characters into their respective boxes for reuse again. The Linotype machine consisted of two chambers. The typed material i.e. typefaces as the matrices which would be lined up and hot lead alloy chamber that forces the liquid alloy to fill the matrices to create line of text. Once the slugs called line of letters (words) are formed, the matrices would progress back through the second chamber of the machine fitted with special keying system that enable the matrix to drop into the correct storage slot, ready for reuse and the process continues till the entire matter is composed, cast and distributed back like a cycle of operation. The possibilities of one character getting mixed up with the other is avoided. Mergenthaler Linotype dominated the printing industry through the twentieth century. The machines were so well designed that the major parts remained virtually undamaged for several years. It is noteworthy to mention that at the time Linotype machines were introduced, the process of Offset printing too started gaining momentum side by side.
As I mentioned earlier, after composing the main text material, the need to insert bolder, bigger sized heading and subheading arose for whose purpose mechanized machine called Ludlow machine was introduced. In early 19th century two Europeans namely William I. Ludlow, and machinist William A. Reade worked hard to device the new Ludlow machine. They formed Ludlow Typograph Company in Chicago in the year 1930 to manufacture a simpler and cheaper version of Linotype for type composing to print by letterpress machines. The Ludlow technology was also based on hot metal typesetting as the device cast bars, or slugs carrying moulded typeface out of lead metal. Those slugs were used for the actual printing, and then melted down again for recycling. The composed matter was also in a single line similar to the one produced on Linotype Machine. The Ludlow machine was extensively used for composing the headings and inserted in the manually composed text material or inserted in the matter on slug already typesetted on the Linotype machine. The Ludlow machine was companion typesetting machine to Linotype and hand composing primarily meant for setting headings in the 20th century.

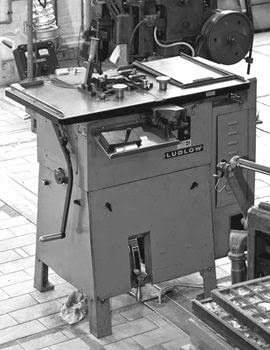
Ludlow machine and composing
stick carrying Ludlow types
Following the success of both Linotype and Ludlow machines, in the year 1911-1916 another International Typesetting Machine Company namely Intertype Corporation was established to manufacture line casting (typesetting) machines which were similar to Linotype machine, but incorporated with several other improvements. The Intertype machine also incorporated with a keyboard, a magazine that contained continuously reusable type matrices, a casting mechanism, and a distribution system for returning back used matrices into their respective magazine, all similar to Linotype machines.
In fact most of the Intertype machines were rebuilt Linotype machines, but modified with several inbuilt improvised features. The advantage of Intertype machine was that it could take up higher point size even up to 30 points which was not possible in Linotype. It was also made possible to use Composing stick attachment to cast headings up to 60 points in size. In fact the machine was highly popular in mid 19th century and they were the first to produce photo composing machines in which photographic films replaced brass metal matrices to bring into picture the term photo composing.
Inter type typesetter machine
Following the success story of Linotype, Inter type and Ludlow machines the industry saw the invention of individual type casting typesetter namely Mono type typesetter machine. In 1890 an American namely Talbert Lanston invented a mechanical typesetting system that included the basic 120 letter keyboard to type the text and a separate caster to mould the typeset matter. Text entry and casting were separately performed in two different machines. The text matter was composed on typesetting machine (Mono type) which produced a perforated paper roll that would indicate the characters as well as spacing required in-between in the form of perforated paper roll. After making necessary corrections the re perforated paper roll was inserted into the Mono type casting machine that produced metallic text matter consisting of single characters instead of a line of slugs like the one produced by Linotype and Ludlow machines. Due to casting of individual characters the process of carrying out the corrections in the composed text material even during the stage of printing was made possible.
The Monotype typesetting machine consisted of 120-keys on the keyboard, a caster, and a replaceable matrix case and divided into quadrants (Four different type faces), each holding one complete type font. It enabled the operator to select characters from any quadrant and mix the typefaces among the four fonts available on the machine itself without picking up font from different cases, offline. The operator typed out characters and spacing to produce perforated roll of paper to indicate characters and spacing. The ribbon was placed on the caster, which read the perforations and automatically cast the individual characters in succession. Since Monotype offered more flexibility in configuring fonts it was well suited for book production that required extended set of characters.
Mono typesetter machine and caster
The Linotype and Monotype corporations slowly plunged into the market of converting the mechanically operated typesetting machines into Photo composing process aided by the computer to directly get the typeset matter on films for reproduction by Offset process of printing which was slowly replacing the Letterpress process of printing from Newspaper, Periodicals printing and to other book publishing. Similar to the eclipse of hand composing which was replaced by Mechanical composition, the mechanical composing too started fading away from the composing sphere leaving the space to Photo composing processes.
However during the mid period – between mechanical composition and photo composing- another process of composing was silently emerging side by side. Called Cold composing the Electronic or electric power operated typesetting process was extensively used by the small Offset printing presses when the Offset printing process was gaining momentum. During the 19th century itself some of the Offset machines like Rota print , Multilith and Romayar baby Offset machines which were nicknamed as glorified duplicators extensively came in use in in-house printing plants of by many firms.
Those machines could print with specially prepared paper plates on which the typing could be directly done using the Electric typewriters that had special ribbon to type the matter. Besides, the images could also be directly transferred by Xerox process on to the plates. The Electric typewriter machine typed text matters were added with illustrations and other headings in bold wherever needed and the same transferred on to the plate by Xerox process. These machines eliminated the use of metal plates and other plate processing involved in the plate preparation prior to printing.
Therefore the Electric/ Electronic typewriter machine composed matters were widely accepted against hand composing or mechanical composing process. The cold composing itself was on experimentation with several new machines inbuilt with new processes coming up one after the other which too culminated into photo typesetting or Photo composing process of reproduction in later years.
The electric powered typewriting machines with typefaces similar to printer’s type for use as composing machines were developed by some of the firms. Few reasons that prompted the development of electric typewriters were:
- Speed up the composing work
- Reduce labour cost involved in type setting
- Quicker reproduction of documents in in house printing
- Easier reproduction on baby Offset machines as plates could be directly typed and printed
Machines based on the Hammond office typewriter design were sold under the brand name Vari Typer from 1927 until 1977-78. Vari-Typers were not ordinary typewriters but composing machines that generated professional looking camera-ready masters for offset printing. As on the Hammond, one could easily change the type-shuttles on the Vari-Typer to type in different fonts and languages. Several models of Vari-Typer machines came into the market that made it possible to give right side justification, letter spacing and variable line spacing machines. It was possible to get perforated paper rolls simultaneously as one typed the text material on paper. After the typed copy is proofread the same perforated paper will be inserted on one side and a new perforated roll with corrections prepared. The Camera ready copy was thus obtained.
Along with the Vari typewriter came the Flexo writer that allowed generating perforated paper rolls while typing the text material. After making corrections, error free duplicate perforated tape could be taken and they were fed into the electronic typewriters to get the manuscript for photographic reproduction process or multiple copies of the text got printed on the same typewriter machines by re feeding the corrected perforated tape as many times as the no of copies were needed.
Flexo typewriter with perforated paper tape
The ends of perforated rolls used to be joined together by pasting the ends so that the paper roll will automatically reach the end and switch over to the top edge of the paper to print the matter again and again. Additional advantage of this machine was that the perforated paper tape could be loaded in a reader and corrected offline. Though Vary and Flexo typewriter machines partly eliminated hand and mechanical composing for smaller jobs, it could be used only for documentation work and to help the scientific community who wanted reprinted copies on urgent basis which also did not require much ornamented pagination. These machines however was not replacement for print typefaces and was only a stopgap arrangement for execution of small work.
The exact origin of Electric typewriter machine for the composing work is not known. But IBM were the pioneers who brought out the Electronic typewriters for use as composing machine to partially replace hand composing and mechanical composing such as Mono and Linotypes. From the history of typewriters authored by IBM, we understand that the development of electronic typewriters to produce camera copy script with typefaces similar to printing typefaces began in the 17th century based on the development programs of some American and British engineers whose efforts brought out power operated typewriter machines in the year 1914.
However when the power operated machine released in 1924 by an American firm called North East Electric Company did not fully meet entire requirements of composing the texts for reproduction it was realized that it needed redesigning and IBM entered into the field to collaborate with them to take up the task of redesigning the machine. IBM began its venture into typewriter manufacturing with the acquisition of the Electromatic Typewriter Company in 1933.
In 1935 IBM produced its first electric typewriter, the Model 01, which IBM considered a commercial success. The first electric typewriters contained only one electrical component, the motor. In 1948, most of the electric typewriters had carriage return, back spacing, tabs, shifting, and line spacing. IBM continued producing typewriters throughout the 20th century until 1990.
Different models of IBM electric typewriters
with typeface in wheel form
The small Offset and in house printers started using Electric typewriters marketed by IBM for their composing work to print by small offset presses. Several models of Electric typewriters released by IBM were inbuilt with typefaces similar to printing typefaces. The use of electric typewriters in place of metal types that occupied huge space was eliminated, the composing work became much faster and in a short time the documents could be composed and reproduced.
On IBM Electric Typewriters every movement was electrically powered and controlled from the keyboard. All working parts like Carriage Return Key, Tab Key, Back spacer, Shift Keys and Space Bar were operated electrically with instant finger-flick touch. Further the Electric Typewriter took away the fatigue involved in composing work.
Soon the type bars carrying the letters (fonts) were replaced with revolving disc containing fonts to quickly interchange the fonts while typing the texts. Perhaps the cold composing revolutionised with the advent of IBM Selectric typewriter invented in the year 1961 that incorporated with several new features. IBM Selectric typewriter replaced type bars and moving carriages with a typing element which was no larger than a golf ball, and which bore all alphabet characters, numbers and punctuation symbols.
Correction tape(1), typefaces in Golf ball shaped bar
Inside view of Selectric typewriter with ink ribbon
The inked ribbon used on IBM machines that produced the print had longer life than normal inked ribbons. It was the first typewriter machine that permitted carrying out corrections on the typed copies by virtually lifting-off the erroneous characters from the typed copy by the correction ribbon by the tab of a key.
In 1974, with the introduction of the IBM Memory Typewriter it became possible to store everything that were typed and allowed the operator to recall previously typed material for revision. This further speeded up the composing process and carrying out the corrections before pagination was also easier to do.
Different models of electric typewriters
with Memory and correction console
Next few years saw the emergence of varieties of photo composing machines that aided the medium and bigger Offset presses, publishers of News papers and Magazines besides book publishing firms. With the emergence of photo composing machines, the manual processing of photographic films could be eliminated for plate making and instead direct films could be produced. These developments slowly developed into direct to print by digital print technology. Though for several decades Phototypesetting enjoyed the status of successful alternative to hand and other mechanical typesetting processes, this technology too has started declining with the emergence of fully digital systems of printing employing a raster image processor to render entire page to a single high-resolution digital image, now known as image setting.
There are thousands of different typefaces and fonts available to designers, printers, publishers, artists and writers (as well as the general public) today. There are all types of display and text typefaces and everything in between. Most of them are available in a digital format from variety of type foundries and can easily be used, and exploited, with modern computer technology.
Recent Comments