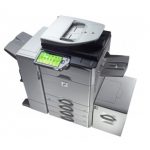
All about printing papers …..2
papers ….. –2–
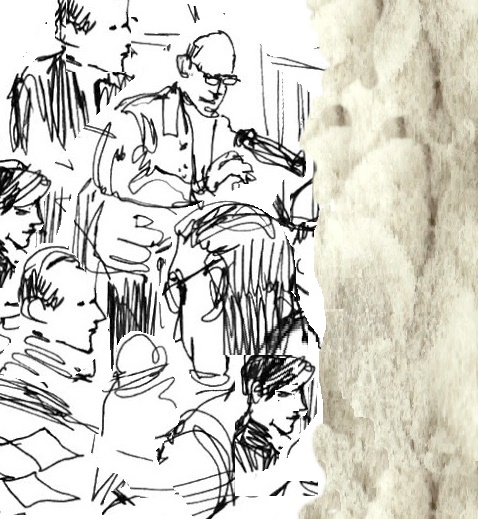
manufacture of paper
Paper is made of a fibrous material. The fibrous material is derived from wood, linen, cotton rags, cellulose fibers from plants and cellulose fibbers from trees which are soft wood in nature. All these materials are obtained from number of sources. Some of the papers are also manufactured with pulp of recycled paper itself. Today high quality paper is made with large proportion of cotton and linen fibbers especially for printing bank notes and currencies. The rags are usually cuttings and waste from textile mills manufacturing varieties of garments and those rags are cut, cleaned, boiled, and beaten before being put to use in the paper mill.
Grass and reeds like Bamboo,Ulla, Sabai etc and plants like Hemp and Kenaf other than the wood are also found suitable for making paper. Because there are many areas in the world without significant forests, Bamboo and Kenaf has been successfully used as an alternate source for making paper pulp. So also are Straw and Sugarcane waste and Flax. Besides the above crops agricultural residues such as Wheat straw, Baggasse, pulp from fibbers of certain fruits are also used.
It is generally believed that the China occupies the top position as manufacturer in the paper and paperboard production keeping nearly 25 % of the world market share in this industry. Certain counties in Europe and Japan follow behind Chinese. History tells us that the paper was invented first in China in the second century for displaying messages to public since paper is the main medium for display of written communication. The earliest paper was made of Papyrus (actually papyrus is not a paper made from macerated fiber but made from a grass like aquatic plant) , the user being ancient Egyptians even though paper was invented by the Chinese in the second century. Prior to communicating the messages by displaying on paper, wood blocks carved with letters or leather Vallam was used in place of paper for displaying messages.
Wooden fibers are prepared mainly from the logs of softwood trees such as spruce, pine, fir, larch and hemlock, and also from hard wood trees such as eucalyptus, aspen and birch. The wooden chips are first converted into pulp of cellulose fibre before put to use in pulp. The paper manufactured with Bamboo is recyclable. Just like paper made from wood pulp, paper made from bamboo can also be recycled to lessen the impact on the environment and to reduce reliance on trees though on flip side there is dispute as to whether Bamboo is a tree or a plant. Whatever it be, Bamboo is used for making paper.
Kenaf belongs to the group of plants of flowers and is potential source for getting good fiber for manufacturing paper. This plant is similar to the tree like cotton and okra and grows well in African countries. The scientist opine that the Kenaf gives unique combination of long and short core fibers which can make them suitable for a range of paper and cardboard products. It is an alternate source to make paper without cutting trees.
The logs of wood generally received in the form of broken pieces or chips or as sheets are broken down into small pieces in the mills and so that they can be converted into pulp in a hydra pulp machine and after completion of the pulping process they are automatically discharged into the main pulp storage tanks ready for processing through paper making machine. The purpose of pulping into a diluted paste is to convert wood into individual cellulose fibers.
Regardless of the type of machineries engaged in the pulping process, the broken wood pieces are crushed in such a manner that the fibbers derived from it remain completely separated from each other. While the log of wood is used in the process of pulp making, the outer bark of the same is not used since fiber cannot be obtained from barks. Those barks stripped out of the trunks are used as fuel in the furnaces in paper mills to reduce fuel cost.
Normally the pulping process is performed in large vessels called hydra pulpers where the raw material in bulk is mixed with several times more quantity of water and then subjected to violent mechanical action of steel rotor blades fitted inside the vessels. Remember, if the raw material is ground into a fine powder they they cannot convert themselves into fibbers to form sheet of paper with crossed fibers on the wire mesh.
Since the basic pulp thus formed will contain several impurities in them, special filtering devices fitted inside the pulper machine remove extraneous materials such as wire, plastic, paper clips, staples etc.
Two different pulping processes are adapted by the paper manufacturers. They vary from mill to mill. The two type of pulping processes are (a) Mechanical pulping process and (b) Chemical pulping process.
In the mechanical pulping process, the logs of wood are crushed into chips by abrasive action on a specially designed mechanical grinding machine as opposed to chemical pulping where the same is dissolved using chemicals. The grinder may be of steel or stone and in order to cool the friction generated heat, water is circulated inside another special device fitted inside.
The expert technicians opine that the yield from the mechanical pulping is much higher than chemical pulping and derived at low cost. The paper produced from the mechanical pulp has better ink absorbency, comprehensibility, opacity, and bulk which are some of the vital parameters needed for good quality of paper. At the same time in so far as the strength for the paper is concerned the paper produced from the mechanical pulp certainly has low strength, low permanence, yellowish in shade primarily due to the presence of high levels of lignin, a natural material found in wood which degrades in colour when exposed to light. It also turns into brownish shade when exposed to sunlight. The lignin is also responsible for reducing paper quality and its permanence. In mechanical process of pulping especially with wood pulp, the non-fibrous constituent lignin binds the cellulose fibers together and therefore reduces the quality and permanence of the paper. During the mechanical pulping process very little quantity of lignin gets removed from the pulp contrary to other processes where the removal of the lignin is significant.
Around 25% of the pulp used by the paper mills around the world is prepared by mechanical pulping process. The papers produced by mechanical pulp is used as Newsprint paper meant to print News papers, periodicals, telephone catalogues, Directories, tissue paper and hand wash towels.
Past few decade development has been the emergence of chemical pulping process in larger manner in which the wood chips are impregnated with specific chemical treatment using sodium sulphite or similar chemicals before converting them into pulp.
In Chemical pulping process, unlike the mechanical pulping process in which the wood is ground by mechanical abrasion, the raw material is subjected to chemical cooking process using chemicals that convert the wood or other fibrous material into individual cellulose fibbers without allowing them lose their natural strength. High-quality papers is produced in chemical pulping process as the process dissolves most of the lignin and liberates the cellulose fibbers thus resulting in better separation of the cellulose fibers. The chemical pulping process produces lower fibre yield than mechanical pulping, say something to the extent of 50-60% compared to mechanical pulping process. The cooked pulp containing chemical is washed and screened to achieve a more uniform quality.
Trees reportedly contain lignin up to 30%, and as said earlier, the material is sensitive to light and turns into brown in sunlight. Therefore in both processes of pulping, in order to dissolve residual lignin to increase the brightness and whiteness of the paper manufactured, the pulps are bleached to some extent with certain chemicals. While chemically treating the pulp to remove impurities and refine them, the process of bleaching is also done simultaneously to take away the dark colour. However excessive bleaching results in decrease of pulp yield, defeating the very purpose of the process. In some of the paper making mills, after the bleaching process or simultaneously in bleaching process certain non-fibrous materials called fillers are also added to increase the cohesion of fibers.
Besides wood, bamboo, plants like Kenaf other refined material like linen, recycled paper, cellulose fibers or cotton combers are also mixed as pulp material for making paper. Water and other chemicals are added and cooked in hot water until the fibers turn soft but not till they get fully dissolved shredding the body of fiber. The hot water also contain base chemical such as lye, which softens the fibers while being cooked.
After refining and crushing the raw materials into pulp, they are filtered and subjected to the effect of machine beaters. At this point, various filler materials are added in the pulped material to suit the type of process for which the paper is manufactured. The filler materials are added to influence opacity and other qualities such as glaze of the final paper manufactured. During this process some alkaline material is also added to make the paper acid free.
The process of sizing remains an important aspect in the paper making process as it influences the strength and printability of the paper. The sizing considerably increases the strength of the paper as well. It converts the properties of the paper from total absorbency into semi absorbent type to the extent that the ink applied on it is only held by it firmly over its surface without getting erased or intruded into the other side to show the prints of front side on the back side of the paper. Sizing affects the way the paper reacts with various inks. They are protective filler that glaze the surface of the paper by filling up the interwoven porosity of the fibers and gives partial glaze over the surface of the paper. Depending on the end use of the paper certain chemicals and materials like Clay, talk, Titanium dioxide, Zinc sulfide, Alum, Rosin, Casein, Wax, Glycerol and Glue are added for sizing, coating and as fillers.
Once the pulp containing undesirable fibrous and non-fibrous materials including lignin are removed, cleaned with fresh water and the other processes such as bleaching, sizing are completed, the filtered pulp material is flown into the paper making machine which has several sections beginning from wet end to dry end. The Paper Machine itself is a huge sized machinery with several control panels attached to it at various points as the pulp has to travel on wire mesh controlled by different gadgets installed in various sections of the machine to maintain uniform flow of pulp. The fibber in the pulp that flows over the moving belt of fine mesh screen gets distributed evenly over the whole width of the paper machine in the form of thin layer of pulp. The semi dry pulp sheet thus formed after getting the water filtered through the mesh screen is squeezed through a series of rollers and suction devices installed. In the wire mesh section, rollers gently squeeze the water from the laid out pulp. The pulp in the form of a sheet, semi wet in condition, further travel through series of heated cylinders which removes the remaining water to give permanency of surface. The computers attached to the machine monitors the movement of the paper as well control the moisture content, thickness, weight, water mark caused through the dandy rollers etc. The above are some of the most important processes carried out in the paper making mills. Several problems that arise due to the behaviour of the finished paper affecting the print quality and control in press room will be discussed at the end. While manufacturing the paper the vital parameters which are to be maintained to meet the requirement of good quality custom made paper are taken care of during the intervening processes. Those parameters confine to the standards of ISO or TAPPI. The manner of testing including the machineries and equipments to be used for testing have also been stipulated in those standards.
Recent Comments