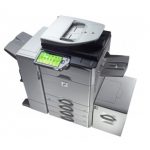
Disastrous effect of Recycled paper – An interesting case study
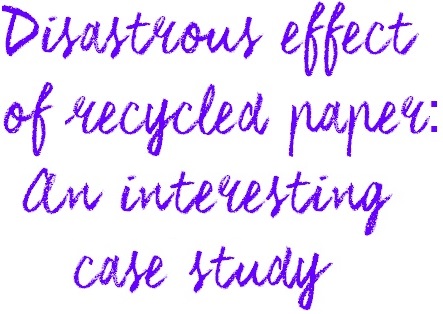
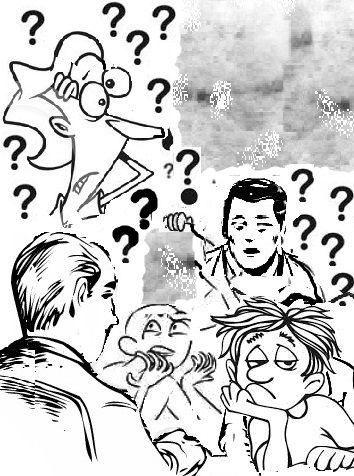
Decades back, few of the most high profile printing units in Asia engaged in the art of printing high value security documents faced a unique problem of lint /fluff problem over the printed sheets which left several voids (white spots) to appear on the printed image during the process of printing in Dry Offset. The high degree of voids appeared as white spots of different sizes on the image of the finished document was unacceptable to the customer as the documents printed were sensitive in nature and had high reputation and value internationally. The problem of voids on print was faced only in the Dry Offset print unit.
The high value document was printed on paper manufactured with 100 % cotton comber (rag content). The paper supplied by the firms contracted though conformed to basic parameters (specifications) of the paper, one of the parameters free from fluff and debris could not be tested at the site of the suppliers because of non-availability of suitable gadget or instrument to test the said parameter. To my knowledge and belief this factor cannot be tested in the lab with only few sheets of smaller size paper unless they were actually put to print trials on the machine using the same quality of ink used on the documents printed to assess the extent of invisible debris stuck on the surface of the paper. Few decades ago, the undersigned had an opportunity to test this parameter on a small table top test equipment called ‘fluff tester’ in one of the reputed labs of a reputed Govt owned paper mill in South India, but the said instrument too did not reveal the true extent of fluff prone paper except indicating to some extent that the paper could be prone to fluff and voids during printing.
The print houses were getting paper supplies from multiple sources of reputed paper mills across the world, besides supplies from local paper mill. Out of several supplies, the paper supplies received from two specific mills were highly prone to the problem of fluff/ debris (void on print) leading to higher percentage of wastage of the printed paper in spite of the fact that the paper supplies were pre inspected before receipt and cleared as acceptable for use, barring for the fluff factor which was only the general specification as it cannot be quantified. The print houses were incurring not only huge loss on profit, but also this problem affected the overall performance of the print houses.
The procedure of processing the documents in those units were:-
- First print by Dry Offset – both old and new versions of Dry Offset machines
- Over printed in Intaglio which partly hid certain areas of print showing void (Fluff) because the Intaglio designs sat over them.
- Examination of the printed documents to weed out the defective printed sheets and sort them as all good and defective sheets.
The Dry Offset machines are generally equipped with powerful de-dusting units inbuilt with anti-static rods which acts to remove the static or surface tension from the surface of the moving paper on the feed board. Once the surface tension or the static is eliminated from the surface of the paper, immediately the suction unit above the static rods under which the paper travel suck off the extraneous particles from the paper surface to allow void free print to take place. Technically termed as static fiction or surface tension on paper is very normal phenomenon in the high speed machines due to the mild rubbing of the continuously moving sheets from the feeder. Even minimum amount of rubbing cause static on paper due to the high speed of machine running, hence the high speed printing machines were always equipped with some form of powerful anti-static devices. This is the general configuration seen on any Dry Offset machine.
In order to keep the production cost of printing as low as possible and to enhance productivity, the permissible printing defect of all sorts was capped to certain percentage of the total sheets printed and processed and workers were suitably rewarded if the end results registered rejection below stipulated capped mark by alert checking during the process of printing to for corrective action of removing the void creating particle before commencing printing again. The capped rejection level in force was in sync to standard norms followed by the internationally reputed print houses who were also engaged in the act of printing similar documents on same kind of paper and other raw material used since some of the raw materials and paper used by them were also received by them from the same sources of international suppliers.
As I said earlier, out of several supplies, strangely the paper supplies from two specific mills were only leading to more and more wastage due to void spots appearing on the printed images which was unacceptable to the customer and therefore those printed lots with defects (voids) had to be double processed which hiked the production cost of the document. In order to control the rejection accruing out of such defect, the machine had to be stopped immediately upon noticing the defect, blanket cleaned to remove the particle stuck on its surface and machine re run. By the time the defect got noticed and machine stopped, not less than 50 to 60 sheets would have been printed carrying those defects. This was unavoidable due to the machine structure.
The internationally accepted norm to maintain the quality of the print material is to run the machine continuously at least for a minimum period of 45 minutes uninterruptedly unless to be stopped on technical issues to take remedial measures. The fluff prone paper did not allow the machine to run quite smoothly and necessitated the stoppage even at an interval of every 10 to 15 minutes which led to huge wastage of print material as well drew the resentment of the workers since the action of removing the voids cannot be carried out on the running machine.
What exactly are void spots and how do they surface? During the process of printing, the inked image from the plate first gets transferred on to the blanket cylinder which in turn transfer the images on to the paper surface.
Let us see how the transfer of debris of Fluff causing voids takes place..
- The unprinted fresh lots of paper, contains partially embedded, invisible paper dust or extraneous particles. They are partially embedded on the surface of the paper as if they have been pasted over the surface of the paper (shown in Red colour). The Blue represents the paper. (illustrations enlarged for clarity)
- When the paper travels through feed board, before entering into the print area, the de dusting unit fitted on the machines sucks off he dust and floating material from the surface of the paper. However they cannot suck off the partially embedded particles.
- When the paper pass through blanket and impression cylinders, the blanket while transferring the inked image on to the paper surface, simultaneously picks up the partially embedded particles from the paper surface and hold it tightly over its surface. When the inked image is again transferred from the plate to blanket in those areas where the paper particles are held by the blanket, the inked image fails to transfer the ink on the extraneous particle stuck because the paper particle stuck on the blanket surface has the tendency to reject the ink like a highly polished particle.
The embedded extraneous particle from the paper stuck on the blanket refuse to get removed by itself and continue to stay over the surface of the blanket, till the machine is stopped and manually surface cleaned, unless the machines are fitted with auto cleaning equipment. The properties of those particles are such that they refuse to accept the inked image making the area no ink acceptable zone, thus finally leaving blank spot on print to appear. Those white spots are called voids or fluff or debris in technical term.
As the problem of fluff/ debris from the paper surface causing void images began to increase affecting productivity several technical committees were formed to find out the basic reason causing such defect. Discussions at several levels were held and matter debated extensively, each group airing their own technical views. Some of the technical views expressed were:
- that the voids were the result of ineffective working of the de dusting unit or less powerful anti-static rods both of which failed to remove the surface tension on paper which in turn held back the floating particles remain over the surface, which subsequently got stuck to the blanket surface.
- improper conditioning of the paper to press room condition
- too tacky an ink which pulled the fibbers from the paper surface
- too much pressure between blanket cylinders
- use of tacky surface blankets
- the machinery and equipment producing paper in the mills were not cleaned properly and the dust and foreign particles stuck on them fell on to the paper surface and got embedded and therefore the machinery were to be thoroughly got cleaned etc.
Based on the recommendation of the committees several tests, trials and other measures were taken with measures cited below:
- Fitment of more powerful de dusting units
- Pressure between blanket cylinders adjusted
- Lesser tacky inks used
- Newer varieties of less tacky blankets tried
- The machinery and equipment in the paper mills frequently got cleaned in the presence of the technical experts committees formed at various intervals.
- A set of paper was freshly manufactured in the presence of committee and tried on the machine.
In spite of conducting tests and trials as suggested, no meaningful result in eliminating the menace was achieved and the end result in every test and trial was almost zero in curbing the problem. Years rolled, none of the observations of the committee members produced concrete results, many of which played less or no role at all on the vexed issue since the root cause lay elsewhere, known only to few authorities in the paper mills that supplied defective paper and the actual fact was kept hidden for mysterious reasons.
What intrigued some of the think tanks were why the paper supplies from the same suppliers with same specification when printed in some of the presses internationally experienced no problem while in the presses referred above in Asia were faced with the said problem of Fluff.
As a test case, when some quantity of paper was produced in one of those two mills under the watchful eyes and presence of some members, the behaviour of those paper were found to excellent on the printing machines. How could then the same machinery and equipment which were blamed to be covered with layers of dust and dirt able to produce in the presence of the members good lots of paper when the basic raw material used was the same? This was unanswered question in the minds of isolated think tanks whose expression of doubts in different angles were brushed aside as irrelevant under certain pretexts and hierarchy. The unfortunate aspect of the entire exercise was that the attention of the committee members were cleverly diverted from the aspect of basic pulp making process and they concentrated only from the pulp filtering stations onward on the paper making process. Therefore for many years the problem of the paper supplies causing voids on print continued to occur on lots of paper received from the two mills without making serious attempt to track the root cause of the problem.
Over the years it became routine affair to constitute few task forces and committees with experts drawn from paper mill, machinery manufacturers and the printing units to address the problem which failed to address the problem as they were mere formalities to divert the attention from the real cause. As an interim measure to artificially reduce the magnitude of the problem, lots of good quality paper received from other mills and defective paper lots received from the specific two mills were mixed and issued for printing in the print houses. The key administrators allowed the problem to die down by itself over the next few years as nobody could offer alternate solution in redressing the problem. After several years when the alternate suppliers entered into the fray, and policy changed, the problem of fluff menace automatically died down considerably.
However the big question that stood unanswered in the minds of thinkers was ‘what exactly was the root cause for the void on print that haunted the presses even though the papers used to be pre and dispatched’? After deeply studying the problem from various angles and discussion with several experts from the same field over many years, it became clear that the root cause of the problem could have been the use of higher percentage (beyond permissible limits) of recycled paper in the pulp process in the paper mill to reduce the manufacturing cost of paper supplies against tough competitors. This fact could not be shared at that time in public, lest it would have created industrial unrest and wrath of key personnel. At the same time the key personnel always believed that time was the best healing factor to hide the facts.
It became clear that in one of the two paper mills, usually the recycled part of the trimmings from their own finished stocks were added with good pulp at some proportion while manufacturing the paper in order to reduce the cost of manufacturing paper. This is usual practice adapted by many other paper mills too. The excess stock of trimmings which remained beyond the scope of their processing unit was sold out.
Few private firms which brought the trimmings from the mills recycled them along with other paper trimmings produced ready to use recycled pulp cakes (paper pulp) and sold them back to the same mill from where they purchased the waste paper trimmings. When the mill faced shortage of main raw material– cotton comber, the recycled pulp cake manufacturers were able to flourish with supply of recycled pulp cakes. The ready to use paper pulp cakes had to be procured by the paper mill to offset the shortage of main raw material due to stringent procurement policies which hit them hard and production had to be somehow kept going even if it meant partial loss on profit, even if it marginally affected the productivity in the print houses. The said paper mill thus knowingly continued production of defect prone paper by mixing good pulp plus some percentage of recycled paper from their own mills plus certain percentage of ready made recycled paper pulp cakes brought from the private entrepreneurs.
The recycled paper cakes contained lots of foreign particles and shorter fibers both of which did not get digested and mixed well with pure pulp. While manufacture, the small extraneous particles which passed through even filtering process lay embedded over the surface of the paper. Those partially embedded foreign particles struck on the surface of the paper have been the culprit in producing severe fluff/ debris problem leading to void images on the print. Nobody seriously bothered to analyse the true causes when the paper mill continued to maintain bad supplies for print houses.
In the case of the second mill whose supply was terrible, it was speculated that the supply of defective paper manufactured with higher percentage of inferior quality raw material was borne out of bad business practice. Gelatin was used by this mill for coating instead of PVA since it was cheaper raw material. The Gelatin too has lot of extraneous particles that prevented proper bonding of fibers especially on recycled paper. It was observed that the paper mill supplied defective paper lots with Gelatin as coating material instead of PVA coating, pulp mixed with more percentage of recycled paper in their supply thus indulged in unfair trade practices possibly due to the following reasons:
- To offer paper at lower rates in the face of stiff tenders.
- To reduce cost of manufacturing paper supply them at lower rate
- To recover recurring extra expenditures, extraneous considerations etc incurred on invisible cost expend while getting contract.
- To offset the extra expenditure expend on subsequent inspections
However years later one of those two mills was blacklisted from supplies later for many reasons. The speculation and observations on both the mills which supplied bad quality paper as discussed above have no documentary proof and were heard to be so. But it was unofficially known that the key personnel were definitely aware of the causes for the bad supplies since the supplies received from other mills who manufactured paper with similar processing techniques, with same specification were able to supply very good quality paper surprisingly to the same kind of print houses.
With passage of time, when passive authorities left, bad suppliers blacklisted and changed, the menace of bad paper supply, mainly due to mixing of recycled paper with good pulp for manufacturing the paper sharply fell down automatically. As years passed everyone had also forgotten the turbulent periods of the episodes. However an important lesson learnt was that when too much recycled paper is added in the paper pulp during manufacture of quality product required for production of high value document as was needed, they will indeed cause productivity loss.
Recent Comments