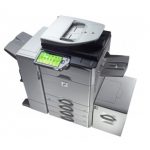
Digital printing
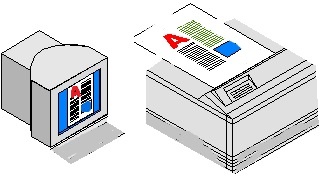
Digital Printing
-N.R. Jayaraman-
Printing technology is developing at a rapid pace and in this direction many of the centuries old practiced conventional processes have vanished. Therefore, it has become imperative for the large and small print houses to update themselves on the latest developments in the print industry. The fast emerging recent developments in printing technology is high-speed ‘on demand digital printing’, ‘three-dimensional printing’ and ‘hybrid print processes’.
Earlier the print industry was reluctant to accept very small quantities for print, and unavoidably if accepted, their cost was fixed based on the minimum order level needed by the printers. This practice proved economically not viable or acceptable to many independent persons and small business houses whose needs were only small quantity of print material and therefore unless it was absolutely essential they avoided going in for printing and instead got them typed or xeroxed till the digital printing systems emerged.
Digital printing is done from a digital-based image directly on to a variety of media. Digital printing doesn’t require plates or blocks or wet inks like the ones used in regular printing processes and instead use dry toners in three to four different shades for reproduction. The coloured toner used in place of wet inks is finely ground powder which gets fused or melted to stick to the surface by mild heat while forming the images on paper or any other media on which the print is taken. Te digital printing proved to be boon to the small print requirements and came to be called as ‘on demand printing’.
What is ‘on demand printing’? The ‘on demand printing’ is referred to digital printing which made it possible to print brochures, mails, labels etc. on need based basis at short notice, across the desk deliverable one, meeting the requirements of professionals and other industries who needed prints in few hours. Therefore, the coinage of ‘On demand printing’ for digital print system came into being. With the advent of newer forms of education and project needs, the demand for very few prints for use on personalized projects or need for last minute stickers for gifts or mementos and display posters in many sizes became routine need. Few amongst the needs were even one or two prints only and thus ‘on demand print’ began to be practiced widely. The ‘on demand printing’ reduced use of paper resulting from unused copies which had to be otherwise printed as minimum print order level. There was also ever growing demand among consumers for affordable yet high quality printing and this trend has been observed in the home segments and students. Thus as the practice of print on demand became regular affair, Digital print system began to be widely used, features of which also aided environment policy as well.
Initially when printing technology expanded after taking off from Letter press printing, slowly the wet Offset process began to gain in, as the need for printing began to be for bigger stocks like posters, banners and other advertising material besides magazines. The mass production of books and magazines’ illustrated with pictures aided the expansion of Offset printing. As the technology began to modernize slowly and steadily, the decline of Offset too began due to the time consuming process and longer workflow involved. The print of smaller quantities were also not cost-effective in the midst of competition in the industry. One other reason was the minimum order level required to execute the job at high cost by Offset process. At that point of period, the digital printing emerged in the form of Xerox and expanded with improved versions of copiers to print black and white to color and thus intruded into the market area occupied by Offset.
The Ink jet printing, the first phase in the Digital printing technology was found to be much faster sans the intermediate workflow processes such as composing, page make ups and then filming on graphic films, retouching etc besides making plates to print them. The commercial inkjet printers offered faster, more reliable and higher quality of work even for the shortest runs which could not be undertaken by the Offset or Letterpress print processes at the cost at which the inkjet printers provided them. The high speed inkjet printers were capable of rendering text at a speed up to 4,000 words per minute combined with incorporation of images and graphics.
Speed and faster delivery alone were not the two main factors that support growth of Digital printing technology, but their ability to render much more intricate designs which the print houses could not offer in shortest period of time strengthen their case. The Digital printing technology offered varying surface finishes of the same designs, high depth three-dimensional graphic designs etc.
The Digital print technology came as a boon to the packaging and pharmaceutical industry where the variable data print labels and cartons were needed for packing the material. The printed brochures, advertising print material, posters, banners- all of them whether very few in nos or medium in quantity could be easily reproduced by the Digital printing machines at a faster and economical rate compared to other print processes as it was capable of producing the printed material directly from the computer files. Further the Digital printing was seen to be reliable and even midway after printing a lot, the last minute revisions and changes needed could be incorporated within few minutes which were not possible in other print processes. Increased personalization of digital printing help make prints more targeted for the end users.
This does not mean that in future the Digital Print process will completely wipe out the Offset process of printing which is the only direct process comparable with digital printing. Print industry watchers believe that both the Offset and Digital printing will have to co-exist as complement to each other, sharing between them short to large quantity of prints, each in their own way as long as commercial printing such as large quantities of Stationery, Legal documents, Newspapers and Magazines continues to grow which are required in print form for majority of people even now.
In short the few advantages seen in Digital printing is :
• It is best suited for printing small quantities of jobs.
• High quality print available on demand in the shortest time possible.
• Paper wastage is avoided.
• Matching true color is easily done
• Time consuming intermediary processes and steps eliminated.
Compared to the conventional printing processes the digital printing offers improved levels of service to the customers both in terms of money and in faster delivery of finished product. Especially the printing requirements of packaging industry, industries which used flexible, metal and corrugated boards are also well taken care of by the digital printing. However There are certain limitations too in digital printing compared to the conventional printing. As per the printers’ opinion, the metallic inks and UV curing inks does not reproduce well in digital printing and in this area they suggest sticking to only conventional printing process.
One of the best and latest feature available in the digital print process is the erasable technology ( I have already written a lead article on it separately) invented by M/s Toshiba. It allows the reuse of the same printed paper again and again after machine erasing the previous prints and to print fresh prints on a special machine supplied by them which works with digital printing. Similarly the errors in print can also be removed and the error removed matter is printed on the same printed paper which is one leap forward in the growth of digital print technology.
What a big change the Digital printing has effected was the elimination of several steps involved in the conventional printing process whenever new designs were to be printed from scratch. In the conventional printing either by Letterpress of Offset the process of reproducing a new design begins with color separations, ink mixing, plate or block making, several modifications based on print proofs before final print approvals which unnecessarily incur wastage of manpower and money especially when ink density and color had to be perfectly matched to the satisfaction of the customer.
In the digital printing process color is controlled digitally to achieve a consistent color match without the need of manually mixing the colors to arrive at the shade to satisfy the customer as most of them are automatically corrected by the computerized control consoles. On desktop the customer is instantly shown the final output and modifications done in minutes seeking approval. The proof will accurately match with ‘to be finished prints’. Once approval is taken the desired print is supplied in the next few hours if copies are very few.
Recent Comments