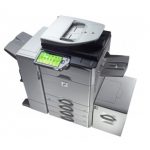
Guide to Printing Students -24
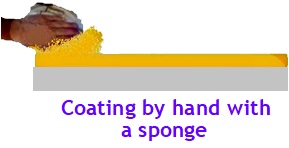
-Few objective Questions and answers-
Written by : N.R. Jayaraman
104) What is meant by Surface Plate making in printing ?
There are few processes by which the plates for Offset Printing is prepared. One such process is called Surface Plate making. Surface Plates are made either on grained Zinc or on grained Aluminum or on Anodized Aluminum Plates. The sensitized Albumen or Casein coated plate, sensitized with Bichromate is the most common form of surface plates. The dried Dichromated Albumen or Casein coating, both of which are protein material gets chemically reduced during exposure to turn into insoluble harder material insoluble in water and at the same remain ink receptive. The areas on the plates that are not covered by the hardened protein material remains water receptive. This is the principle of Surface plates. The image thus created stays over the plate surface, almost merged with the grains on the surface of the plate as a thin film.
105) How is the Surface Plate prepared?
A surface plate is prepared in the following manner:-
- The required plate is well washed with mild Acetic or Phosphoric acid, Hydrofluoric or Hydrochloric acid solution to clean its surface and washed well with water before coating. This process is called counter etching.
- The counter etched plate will be fitted on the whirler, locked on all four corners and switched on to rotate in medium speed.
- The readily kept sensitized bichromated albumen or bichromated Casein mixed with ammonia coating solution will be poured in the center of the plate in slow motion and whirler speeded up to ensure that the coating solution evenly spread on the entire plate in dark yellow lighted dark room.
- Since the mixing ratio of the coating contents differ a lot from product to product, the present day printer prefers to use the ready to use sensitizer coating available from the manufacturers of coating and developing solutions.
- The whirler will be allowed to run till the coating gets dried. Once dried, the plate will be taken out and after cello taping the negative over the plate in the correct position as per the layout, it is locked in a vacuum fitted exposure frame after covering the non-image areas with black paper. Remember that the plate is exposed only through a film Negative and not film Positive since the plate areas exposed to light becomes the image areas. For preparing a plate with positive, a different other coating is used. In the negative only image areas remain transparent to allow the light to pass through while the non-image areas remain fully black preventing passage of any kind of light.
- The plate in the fully vacuum frame will be exposed to suitable U.V. light source for stipulated time (few minutes) which is gained by experience. The exposure will ensure that the areas exposed turns into hard coating leaving the non-image areas remain unaffected.
- Once exposed, the plate will be removed, placed over a table and special greasy ink applied over the image areas and well rubbed to ensure that the hardened areas absorb the ink and turns into ink receptive areas.
- Prior to applying the developing ink, a solvent called non blinding lacquer is applied over the exposed areas to ensure that the image areas get strengthened for ink receptivity.
- Then the plate will be washed with water to remove the unhardened coating from the non-image areas leaving the image areas visible in black colour over the plate.
- After washing the entire surface of the plate well and surface allowed to dry, finally the plate will be thoroughly gummed to ensure that the non-image areas do not get oxidized. The gum reacts with the plate to form a chemical layer that will prevent oxidation of the plate surface.
- The gummed plate will be ready to fit on the Offset Printing machine for further processing.
The quality of the print is higher and the plates made by Surface Plate making process runs with sharp image for few thousand runs, say even up to 25,000 copies without giving any other technical problems. Thus they are preferred for medium run copies.
106) What is the purpose of counter etching and which chemicals are used in counter etch solution?
Counter etch solution is a chemical cleaning process for the metal plates (zinc or aluminum) before a plate is coated with a sensitizer solution to create newer image. The counter etching, which in effect a chemical abrasion process, is done to remove the effects of protective gum film those which remained on the previous printed plate. Even though the plates may have been grained to remove the previous images before processing for fresh imaging, due to the adsorbed gum film which sometimes remains over its surface may reduce the grease or ink receptive tendency of the plates. In order to ensure that the plate remains fully ink receptive to hold the freshly created images on them, the counter etching process is done. At the same time the counter etching chemicals should not be strong enough to damage the grains on the plate.
Generally Phosphoric acid, Hydrochloric acid will be added with water in certain percentage for use as counter etch solution.
Recent Comments