29. Specifications : Specification means the series of parameters pertaining to a specific material or product used/procured. Every material or product has several qualities and in order to ensure that the product in demand meet the requirement for which it is intended, the product profile or characteristic is given in detail which is known as Specs or Specification.
Similarly in printing too the material procured is done by clearly expressing the material qualities. For example the Paper has several qualities such as Absorbency level, Porosity level, Tear resistance, Double fold, Strength, Pulp content, Lab value, Thickness, GSM, Elongation etc relevant to the specific print order. The parameters will be given in detail in the tender and tested in the laboratory before acceptance.
Similarly for printing machines the Specification includes the Size of the machine, Floor area, Max speed, Configuration, Type of Feeder, Voltage required, operating system preferred etc, etc. The tender specifications will indicate all the requirements in detail.
30. Spectrometer : The Spectrometer is an instrument which measures the amount of light of a specified wavelength which passes through a medium. This is only theoretical information to Presses and has more relevance to analysts and researchers.
31. Split Run : Split run means printing of an image with different themes in different editions (different Geographical region or same area but different locations) of the same publication like Magazine and News Papers. May be in Minnesota edition it will be image + X, Washington edition the same image will appear with with another text and in New York edition it could be the same image with another text. This kind of variation inserted in the advertisements and printed on the same date and same publication are called Split run.
Some time even the entire matter and images may be changed. This is one of the techniques deployed by the advertising agencies to test the impact of the message in the Advertisement to formulate wide acceptance of the advertisement contents to be inserted in future. Split run is also called a market study or survey as is called.
Also while printing a book, the same matter is printed in different manner meant for Deluxe edition, Library edition and paper book edition under Split Run. Some times even the same pamphlets or brochures are printed in several colours and such work is also called Split run. For example when the pamphlet or brochure for family planning gadgets are printed for mass distribution, it may be printed in different colors and different languages say three ups in a row with split fountain. They are also called Split run.
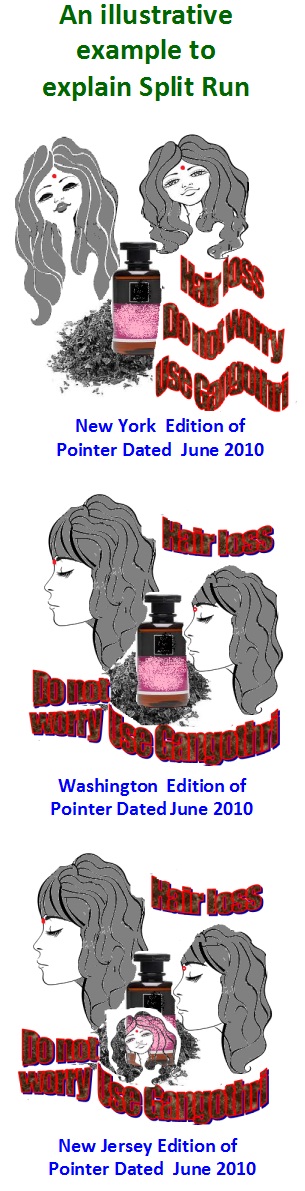
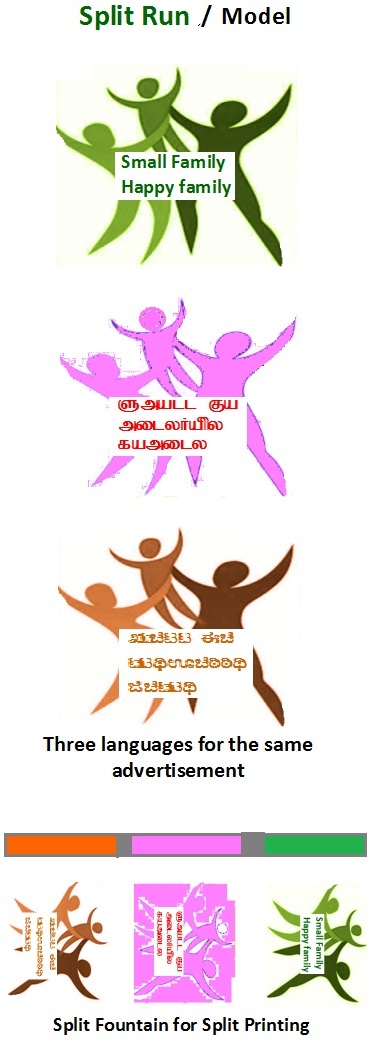
32. Spoilage : During printing or any manufacturing process, there will be additional production other than the actual requirement. The additional production may not be all good production, but are meant for make ready before running the final production. The additional sheets are also meant to stabilize the settings for the main production. This is an universal accepted mode in production field. While printing some job additional sheets are to be printed to make the settings perfect to print the actual quantity required.
For example when 10,000 copies of a booklet containing four colours are printed, the printer will print additional 100 to 200 copies or so as spoilage. This is done to register the next colour on previously printed sheets, for feeder adjustment, color adjustment and for make ready for subsequent printing etc.
There are many different manufacturing activities within the production process such as two sides printing, trimming, folding, collating, stitching, etc. In the course of each production task, some quantity of printed sheets will get wasted. Therefore to eventually hand over the ordered quantity, additional copies have to be printed to compensate loss in the above said activities out of which some are recoverable as good copies. However they may be offered to the Customer if he is willing to pay for it at discounted or negotiated price or destroyed.
The main question one may ask is how much is the spoil percentage allowed ? There is no fixed percentage to spoil percentage because it depends on the efficiency of the presses to control the spoil percentage to gain more profit. However the universally accepted norm is 10% spoilage for normal production and if the volume of run is huge, then the spoil percentage should be maintained below 2.5 % for normal quality printing and up to a maximum of 5% for high quality printed work.
33. Slip sheeting: Slip sheeting is another name given for interleaving process. This process is inserting a sheet between the two printed sheets to prevent the ink from the surface of the previously printed sheet getting transferred on to the back side of the previously printed sheet. Such slip sheet is called interleaving. Read more under Interleaves or interleaving in Alphabet –I.
33a. Scumming :- During printing by offset process, sometimes some of the non-image areas of a plate become receptive to ink, and transfer weak tint like colour on to the paper which is called scumming. Ink adheres to non-image area of the plate during the press run and cannot be removed using a damp sponge. Sometimes the scumming may be seen only in some areas. This defect is caused by a variety of press conditions such as fountain solution that is too acidic or too alkaline, leading to desensitizing of the non image areas to become partially oil receptive (Improper PH of fountain solution). Few other causes are:
- Improper graining -coarse grain- of the plate.
- Poor plate making process adapted during plate making.
- Plate may have been partially exposed to light after coating.
- Fountain solution highly bichromated
- Glazed blanket/plate
- Excessive printing pressure
- Ink body too soft
- Improper dampening unit settings for dampening the plate.
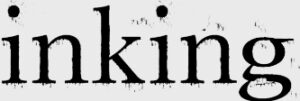
33b. Smashed Blankets:- Sometimes during machine run, some extraneous particles may come in between the blanket and the plate or the impression cylinder and damage the blanket. Some times the paper with fold when unknowingly fed causes this problem. In such cases the blanket will not produce the print properly as the impression at that point may not be proper and print will show weak image on that spot.The blankets affected thus are known as Smashed Blankets.
They can however be partially repaired by under packing the blanket at that particular spot or treat the blanket with some solution to swell the area to regain its thickness since the Offset blankets are made of layers of rubber and fabric in between. When the number of rubber layer is more on the blanket, the chances of it getting smashed will be much less as the rubber has elasticity to compress and regain its surface like a sponge.
………..Additions to alphabet S to be continued under S/8
Recent Comments