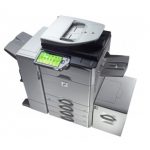
Alphabet -S /4
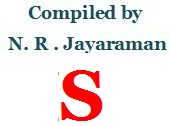
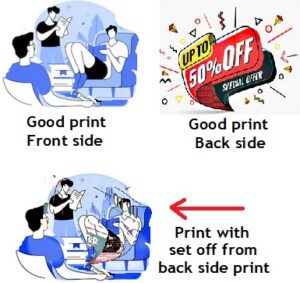
18. Stretch ink: This is a very special quality of ink supplied by specialist ink manufacturers to print on the substrates and surfaces which will stretch or shrink after printing. In such an event the printed image will show cracks on itself when the substance or the medium on which the ink is printed. Therefore to tackle this problem the Stretch ink is used on such material which are liable to get stretch during use. Such special inks are called Stretch Inks and they possess elastic tendency to stretch with the material on which they are printed. Example of such inks are those inks used on stretchable Fabrics.
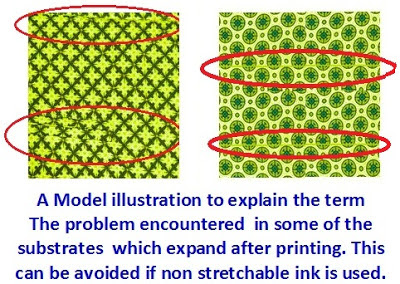
19. Shrink wrap: Packing the material in tight pack with the use of plastic or PVC or Polythene film is called Shrink Wrap. The material to be packed is wrapped around by the plastic film and pushed into the heat chamber. Due to heat the plastic film slightly melts and shrinks into a bundle. The heat chamber is so designed that it does not burn the film, at the same time ensure that the film gets shrunk tightly and adheres with its own surface. The shrink wrapping is done by automatic machines which automatically wraps the material with a layer of thin plastic film and shrink wrap it. This clear shrink wrap is used for packaging of many products including bundling of Currency notes.
20. Surface Plate :- There are few processes by which the plates for Offset Printing is prepared. Out of many techniques employed to make a printing plate for Offset machine is the Surface plate making and the other is deep etch plate making process. The Surface plate making process involves coating of Aluminum or Zinc plates with light sensitive albumen, or gelatin or Casein material. The plate is then exposed with a negative. The image areas become hardened and insoluble to water or other liquids, while the non image areas remain un affected. The plate is then applied with an ink which makes the hardened areas ink receptive, while the non image areas with the coating remain unaffected. Then the inked plate is developed with water and all the non image area coating, which remained unhardened gets washed away leaving the hardened image areas on plate. The plate is then gummed for using it on the Offset machine. Since the image areas lie in the same plane with non image areas, the process is called Surface plate.
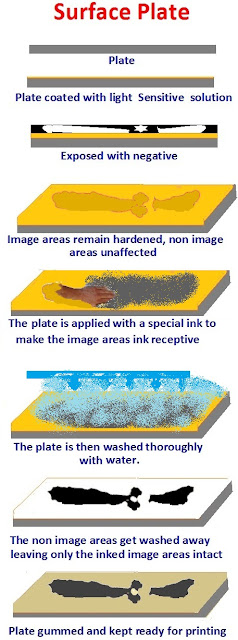
Recent Comments