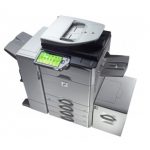
Students guide for Printing -42
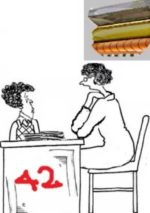
-Few objective Questions and answers-
Written by : N.R. Jayaraman
183) What is Cold set and Heat set printing process?
Cold set printing is the process in which the printing ink dries gradually into the surface of the paper by evaporation and absorption without need of heat application in any manner to dry the ink. This type of printing is best suited for printing on absorbent papers. Uncoated stock of papers such as newsprint, bond and book paper are best suited for printing by this process. Most of the News Papers and Magazines are printed by Cold set Process of printing which is also cheaper compared to Heat set process of printing. Since the ink does not immediately dry and partially remain wet over the surface of the paper for sometime, but at the same time without causing set off on the back side of the papers, one will experience residual dry ink leaving mild traces of blackness over the hands of one handling the newspaper. Sometimes the use of cheaper ink may also cause such problem even after the printed stock is dispatched several hours later.
Heat set printing is the process in which the printed ink is dried by passing the printed paper through a heat chamber before the printed paper enter into the delivery board. The oil based solvents in the ink reach evaporation point called flash point as they pass through heating chamber followed by chilling rollers. Once the printed pages are inside the cooling chamber the ingredients in the ink cools down and solidify or set on the surface of the printed material. This process of printing mostly using gloss inks gives a cleaner print. Coated paper or paper with Glossy surface as those used for printing high quality magazines, flyers and Product catalogues mostly go through the printing by heat set process because the surface of the coating does not allow full absorption of the ink into the paper before they entering into the delivery board. Lest the ink set of problem will be faced on the printed stuff.
184) What is Segmented Roller and Segmented Blade? What are their advantages?
Before understanding what the segmented roller and segmented blade is and their importance, it is necessary to briefly understand the configuration of the inking system where they are incorporated.
The inking system on any printing machine consists of several rollers including group of form rollers which supply ink to the printing plate. The form rollers get the supply of ink from series of rollers which get the supply of ink from the intermediate roller called duct roller, which is an important constituent in the inking system.
The Ink trough with a fountain roller fitted with a slightly flexible fountain plate has several keys on its back to control the supply of ink fed on to the roller chains. The duct roller which is the crucial linking roller between the fountain roller and the chain of inking rollers transfer the ink from the ink duct to the chain of rollers. The uniform and required amount of ink transfer from the ink fountain plays the most important role that determines the overall print appearance.
In the conventional ink duct system the ink supply from the ink duct is controlled using control keys fitted on the back of the duct. The gap between the duct blade and the fountain roller is increased or decreased by tightening or loosening the keys thereby allowing the precise quantum of ink flow from the duct to match the needs of the image areas. However the precise need of ink to certain areas cannot be controlled in the conventional ink duct system in the manner one can control on the segmented roller system. This is because even after fully tightening certain portions of the duct to stop flow of ink, still certain amount of gap can be seen between the duct blade and the fountain roller through which a small film traces of ink sneak in as can be seen in the illustration shown below.
Therefore in order to ensure precise ink supply from the ink duct to the inking rollers, instead of the conventional ink fountain blade specially innovated segmented duct roller or segmented duct blades are used. The segmented roller have finer cut separating small portion or segment of roller across the length of entire duct roller thereby allowing the operator to precisely control the flow of ink from the individual segments to the needs of the image areas. The finer cut between each segment or equally divided spaced zones (one segment per ink key) allow greater accuracy adjustments within each zone. There are two types of segmented rollers offered by specialist firms.
Segmented Roller – I :- In the first variety of segmented roller system, each segment of the duct roller is mounted off-center over the length of the duct roller which acts in a unique manner in transfer of ink. During transfer of the ink from the duct while some segments of the duct roller are in contact with the fountain roller, the others are in contact with the adjacent drum roller. After a set period of time, the segments switch positions to transfer the ink vice versa. This helps with the uniform lateral distribution of ink across the press. This form of segmented duct roller has been developed before three decades i.e after 1970.
Adjusting the amount of ink sent through the system can be done in two ways. The first is using the fountain keys to control the space between the duct blade and the fountain roller, which controls the lateral distribution of ink. These keys are usually adjusted based on the ink requirements of the particular plate. The second is by adjusting the ‘dwell time’ (amount of rotating time the duct roller keeps in contact with the fountain roller) so that only a thinner even coat of film of ink gets transferred on the fountain roller. See illustration below to understand this system of inking.
Segmented Roller – II :- In the second variety of segmented roller system, the segmented roller has finer cut separating a small portion or segment of roller across the length of entire duct roller thereby allowing the operator to precisely control the flow of ink from the duct. Unlike in the first variety, the segments are uniformly seen over the entire length of the roller. The finer cut between each segment or equally divided spaced zones (one segment per ink key) allow greater accuracy adjustments within each zone. With this kind of divided duct roller, it is possible to print solids and spot colour side by side without allowing mix up of inks. See illustration below to understand this kind of segmented roller used in the inking system.
Segmented Ink Blades :- The third version in the inking system is the use of segmented ink blades which help the press operators to achieve the precise ink setting more quickly thereby minimizing the make-ready time, and reduce paper and ink waste. The segmented blade is a flat ink fountain duct blade which had finer laser cut separating several segments of the entire length of the blade so that each portion of ink flow can be controlled precisely on each segments and when in some portions where the ink flow is to be totally stopped by tightening the keys, no gap will be left between duct and fountain roller like the one we can expect in the conventional duct blade system. The one-piece minor laser cut blade clearly divide the segments into equally spaced zones (one per ink key), allowing for greater accuracy adjustments within each zone. See below the illustration to understand the same.
Custom-designed segmented blades are made available for direct replacement of solid blades fitted in the ink fountains of the printing machines of any make. The segmented blade is fully interchangeable with conventional ink blades.The main advantage in these newer developed inking system is the ability to transfer the exact amount of ink required in any zone without compromising other areas of the plate.
All the above mentioned newer developed systems – segmented roller and segmented blades – can also be attached with remote Ink Control System including touch screen system provided such a combined system is opted to enable printers to achieve dramatic reductions in both make-ready time and waste by accurately pre-setting all ink fountain keys. The segmented blades suit more for the remote controlled ink fountain system. One important advantage is that the custom prepared remote ink adjustment system can be fitted on any machine ink duct by replacing the conventional ink fountain.
Recent Comments