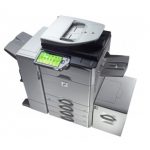
Recent Developments in Printing – 5
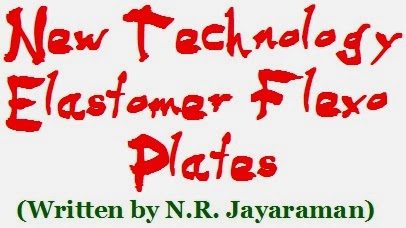
The Elastomer has become an important material for making flat Printing plates or Sleeves for engraving in combination with the Photo Polymer component. The Elastomer is the polymer constituent of natural rubber, which is made from the milky latex of various rubber trees. Natural rubber is still an important industrial polymer, but it now competes with a number of synthetic rubbers which are derived from by-products of petroleum and natural gas. Elastomers are usually thermo sets but may also be thermoplastic.
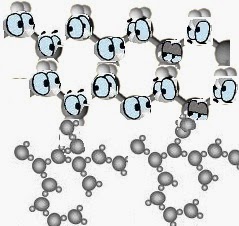
The molecular structure of the Elastomer material consists of several cross links with a meatball like structure linking them together called covalent bonds. The assemblage of linked units is often referred to as the chain and the atoms between which the chemical bonding takes place are said to make up the backbone of the chain. The molecular structure and their behaviour gives the Polymers the properties of extensibility and elasticity and therefore the properties of Elastomer need to be modified by converting the original liquid form into a solid state that will not flow by curing or vulcanizing process. They are then turned into useful Elastomer Flexo Plate materials. The Elastomer is used in combination with certain Polymer substances for use as Flexographic plates or Sleeves to convert them as printing plate. Flexographic printing plates made from rubber provide excellent printing quality.
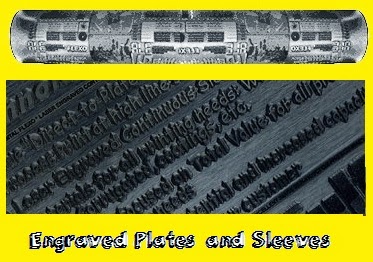
The Elastomer Flexo Plate /Sleeves are taking the Flexographic Industry by storm as the plates have distinct advantages like :
- Lesser processing steps
- Produce superior print qualities
- Cause no plate swelling during printing
- Print 2-6 times longer than Polymer plates
- Enables faster registration
- Short make ready time involved
- Faster machine speeds possible compared to other plates
- Reach color density faster with improved print contrast
- Overall usage cost is lesser than Polymer.
Elastomer plates are mostly designed for direct engraving technology particularly in sleeve form. Developments in direct laser engraved plates have opened new avenues for the flexographic printing industry. Direct engraving has the potential to improve not only the quality but also cost efficient. Start-up waste, registration, make-ready time and print speed all favor the choice of direct engraved Flexo sleeved plates.
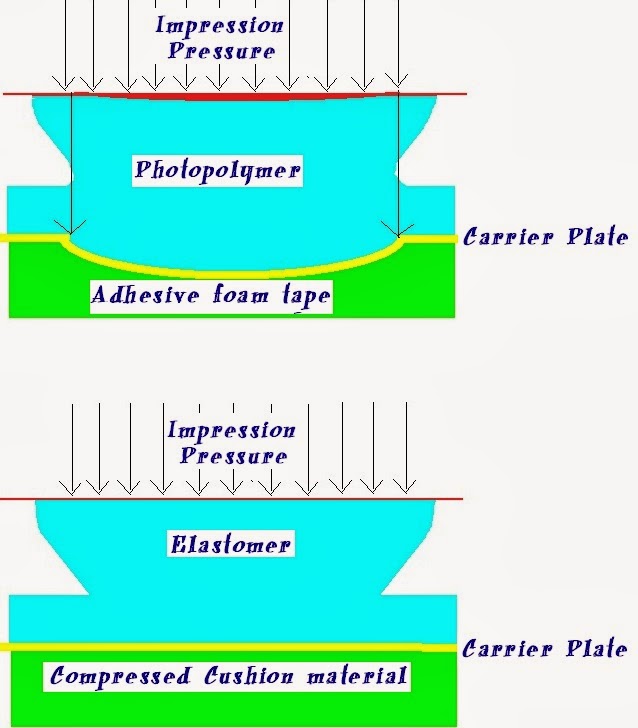
In the recent years sleeve technology for making engraved plates, instead of preparing conventional printing plates has been put to increased use in wide range of graphic and technical applications. The Elastomer sleeves are thicker and more durable. This eliminates the use of multiple plates or sleeves for long runs. Sleeve durability does not just come from Elastomer materials alone whose ability to stand up to press pressures, corrosive inks and cleaning solutions are high but also from the way they are imaged on the engraving machine.
Digital control of the halftone shoulders (blank areas between images) during engraving the Elastomer plates or sleeves contributes to dot stability and reduces break-off which adds durability and consistency. Engravings below the image surface play important role as their shape and depth cause consistent images even if the plate is slightly over squeezed on machines. Control of the shoulder allows to print razor sharp texts even when their size is below 2 points and the ability to print smaller reverse text without filling in. This is where the Elastomer product helps in. Laser engraved Elastomer sleeves have an inherent quality control advantage over normal Photo-Polymer plates. Sleeves can be stored vertically requiring less warehouse floor space.
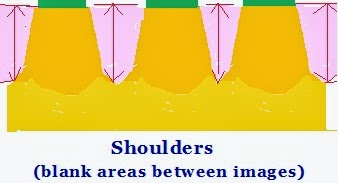
A wide variety of elastomer materials with different durometers and ink lay down characteristics are now available as manufactured by some of the expertise firms around the world. It was observed that higher ink densities could be achieved with laser engraved Elastomer sleeves even at higher press speeds at the same time maintaining print contrast. M/s Eastman Kodak has developed a system whereby all Elastomer sleeves are quickly pre-scanned on the engraver to check for a flawless surface and rejected before imaging if any imperfections are detected.
The laser engraved Elastomer sleeves have only three steps to imaging :
- layout preparation
- engraving
- and finishing
This means that once the sleeves are to be mounted on the machine and command given they are engraved and finished without involving wash ups with several steps and solutions. Photo polymer sleeves have many more steps like
- file preparation
- masking
- exposing
- developing
- washing-out
- drying
- post exposure if needed etc.
Recent Comments