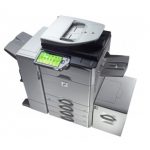
How to cut down Organizational cost – 4
Organizational cost- 4
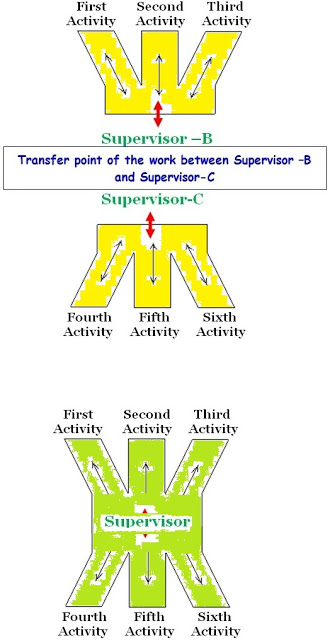
Preventive and predictive Maintenance to reduce cost :
A periodical maintenance program was freshly introduced both for preventive and corrective maintenance thereby helping reduce the down time of the machineries and equipments. Since the Organization cannot afford to maintain a fleet of separate personnel for this purpose, an agency was given annual contract both for weekly maintenance and for urgent repairs. The Contract was so designed that two contract personnel will be posted in the factory everyday during factory working to attend to the repairs. The contract amount though matched with the wages which otherwise would have been paid to normal worker had long term advantage. There will be no liability for the Management on annual increments, gratuity etc for the said group of workers whose work will be limited and except on weekly maintenance days, on many occasions there may not be work at all if the equipments and machineries functioned well. Arranging the spare parts from local market was the responsibility of the contractor on cost basis, even though the essential minimum spare parts will be kept by the Organization which cannot be instantly procured.
Tool Standardization to reduce cost of handling.
Analyze tools used in manufacturing and determine the most common of existing tools. Entire Raw material purchased be standardized to ensure that the quality does not vary while manufacturing the goods.
Standardization of the processes deployed to ensure that there is no deviation from specified process which will result in absolute quality of the end product.
Creation of a pool of workers by identifying the workforce capable of performing the allotted duties upon training. When the pool of workforce is kept ready, you need not fill the vacancy in any department with personnel from outside and easily transfer suitable personnel from the pool which will save the overall cost in wages.
Outsourcing major consumable parts : Advised not to manufacture the standard parts in the factory. To the extent possible outsource those parts which are commonly used. This can be got done by even contracting the same to ancillary units to specified design.
Continuous improvement in design elements : Effecting continuous improvement process for the ongoing major operations by studying the process and close monitoring . A meeting be held every six months to review the process carried out.
Periodical analysis of the quality defects: Frequent collection of quality defects and analyze the reasons to take corrective action.This will also be part of the six monthly discussion group.
Better inventory control : Quality and Quantity control on the stocking of material required in the factory. The technical specifications for goods and related services procured should not prescribe a particular product, brand or service provider, and should include a statement that specifications are not limited to any particular brand or manufacturer. This will give wider supplier audience and to frame up a long supply policy.
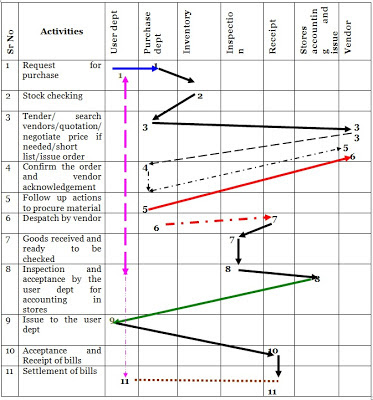
Recent Comments