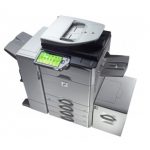
Alphabet- I
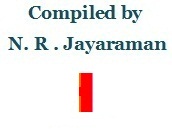
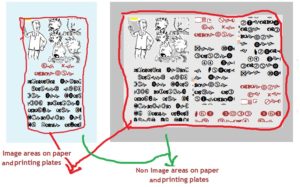
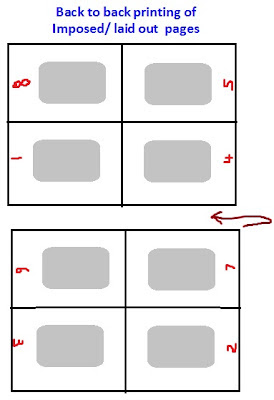
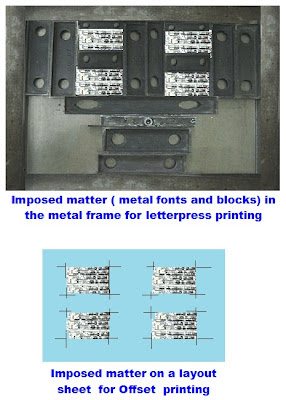
3. Impression: The process of transferring the text and images from the plates or blocks on to the paper or other substances by the process of pressing them tightly against paper to impress the image on to them which is called ‘giving impression’. During the process of impression only one plate with image on them can pass through the impressing medium. When 500 or 1000 copies are to be produced, the sheets will get 500 impression or 1000 impression if individual pages are printed. When the same page is made up in multiple pages in a sheet and then printed, the no of impression will depend upon the no of ups the pages have.
For example when 100 pages are printed as single pages, the impression will be 100 in number. However if the pages are laid out on a bigger sheer in the format of four pages per sheet, then the no of impression will be 25 impressions which however will give 100 pages when cut into individual pages. Supposing each page contains 10 pages then the no of impressions will be 50 for 500 copies and 100 impressions to produce 1000 copies.
While on the platen printing machines the impression device will be in the form of a flat surface called Impression frame, on the high speed rotary machines and web printing machines the impression will be given by ta medium called impression cylinder which will be in cylindrical shape.
4. Impression Cylinder : A Cylindrical device on the printing machine that press the paper against the plate or blanket or assembled composed matter locked in a frame to ensure that the design elements on them gets transferred on to the printable medium uniformly. On most of the machines series of grippers that hold the printable medium in registered position for printing are kept attached to the Impression Cylinder. While in all rotary printing machines, the impression cylinder is not covered with any material and are only bare cylinder, in respect of Intaglio machines the impression Cylinder is covered with a special fabric based material to press the paper effectively against the plate cylinder.
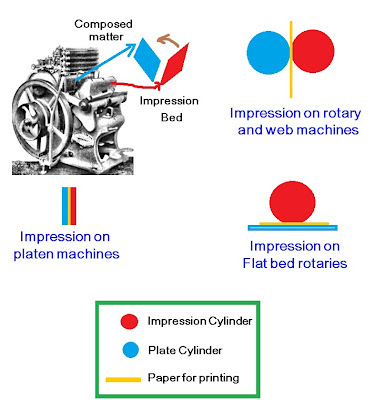
5. Ink Fountain: One of the vital parts, in the form of a duct or tank fitted on the printing machine from where the Ink required for printing the print material will be supplied to the plate or blocks for printing through series of intermediate rollers which grinds the ink further for smooth flow.
6. Imprint : It is mandatory requirement in all the countries to print the publisher’s name, address, edition etc in all the printed books of any nature, either in separate page- generally opposite to half title pages, or opposite to the contents page- or in the last page of the book. Such printed matter is called Imprint. Besides providing such information on the printed books, it is also mandatory to print such information at the bottom of single sheet posters, leaflets, pamphlets etc to identify the printer who printed the matter.
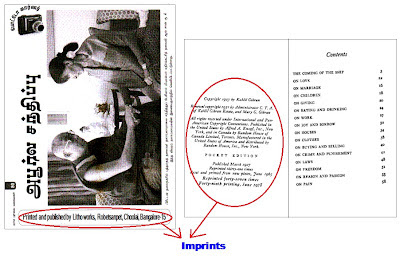
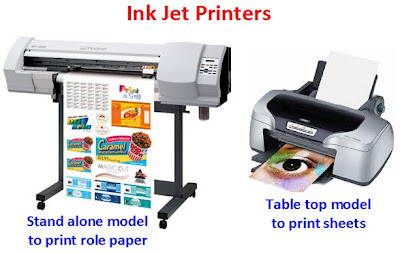
8. In-Plant Printer : The big industrial houses have their own small printing presses to bring out their activities and function in the form of a printed booklet from time to time or get their entire stationery and print requirements printed within their own organization. The main advantage of having such an in-plant printing is that it will require only less man power operate, capable of generating faster information through print media as they will be situated within their own organization. Since the in house printing activities does not include profit, the out put turned out is always cost effective.
9. Intaglio Printing : It is a highly specialized process that gives the document a very high quality of relief images perceptible by touching with the fingers. This is based on one of the oldest processes in which the prints were taken from etched or engraved copper, zinc and steel plates to give relief image. This process of printing is widely used as the one of the best security features. The oldest process has been subsequently improved upon drastically to cause relief images from different technology generated processes and plates printable through the rotary printing presses.
The major disadvantage of this process of printing is that the multi color images can not be reproduced by this process, and only cut color printing, that too with limitation is possible to reproduce by this process. The reason being, the impression needs to be given with high degree of pressure. The high pressure causes the ink from the recessed image get adhered to the paper. Again if the same sheet of paper is fed to give another impression, the relief effect generated by the first print operation will go down or will become plane due to high degree of pressure given on the paper.
The basic working of Intaglio printing process is as follows.
– A highly stout ink is pushed into the depressions of the plate and the surface is wiped clean, leaving ink only in the recessed areas.
– The paper surface will get pressed against the plate and substantial pressure given so that the paper is forced into the depressions of the plate to produce a richly inked impression.
– On automatic machine the highly stout ink is applied to the recessed areas by specially prepared image cut rubber based rollers.
– The printed sheets can not be quickly used and relief images will have to be allowed to dry for at least 48 hours.
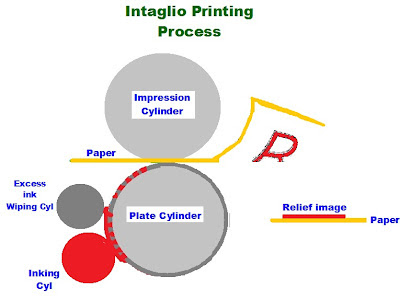
Recent Comments