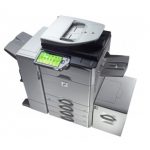
New contact scanning technology for print inspection
New innovation in print inspection –Scanning technology
Lake Image introduce a new contact scanning technology for high resolution print inspection
(Written by N.R. Jayaraman)
All over the world the online print Inspection system is based on Camera based technology. In recent years the camera based sheet inspection system has been replaced by a scanning device which works much faster producing close to the actual requirements. The new scanner based technology called MaxScan reportedly provides a true 600 DPI resolution for print inspection applications either on sheets with widths ranging from 12 inches up to 24 inches or on reel of paper running as web in a width of 36 inches. The additional advantage according to the manufacturer is that the unit operates with its MultiScan toolset that discovers missing or blocked jets in the running machine so that the wastage on account of rejects could be reduced. The aim is to detect any errors as soon as possible to reduce the risk of large amounts of waste product.
The main inspection apparatus MaxScan Linear Contact Scanner inspects the prints from a distance of just 1/2” from above the paper surface. The system, according to the manufacture can be integrated comfortably within the transport system of the machine, without the need for additional rollers, redesigning the web paths etc unlike the standard camera based inspection system that requires complex settings to integrate all the assemblies including optical assembly.
One of the important breakthroughs in this inspection technology is its ability to provide consistent and reflection free images of holograms and foils unlike Camera based Inspection technology camera where each hologram in a row or lane can appear different within the inspection image based on its location relative to the camera position that reads the images.
According to Lake Image Systems Ltd , UK “MaxScan overcomes the above optical phenomenon, allowing the implementation of powerful inspection functionality to guarantee the quality and integrity of even the most challenging substrates”.
MaxScan system provides the highest performance, most scalable print inspection technology in the market. Traditionally an inspection system uses a camera to acquire the image for inspection software to then do its thing. In this case the camera is a linear scanner similar to a very high performance fax machine sensor.
Some of the key advantages of MaxScan according to the manufacturer has been:
1) It has a high resolution fixed over the entire width of the sheet where as the traditional camera has a variable resolution based on its field view.
2) In traditional Camera based inspection system, the inspection of the dots or pixels in print will depend upon the field of view of the camera. If the field view of the Camera is 100 mm, then it picks up only 10 pixels per mm and when the field view of the camera is 200 mm, then it can pick up only 5 pixels per mm. In the case of MaxScan the manufacturer claims that the scanner will pick up over 24 pixels per mm up to a sheet width of 926 mm in size, which is almost three times than the conventional Camera based system.
3) The above has direct bearing on the space required over the sheet travel path of the machine to fit the inspection unit. Where the sheet size is say 500 mm wide, the minimum space requirement above the point of inspection will be 500 mm above, further nearly half of it, say 200 mm to accommodate the camera fittings and wires etc as many no of cameras will be required to be fitted over the entire width and the no of cameras will depend on the field view of the camera interalia dependent on the cost factor of the system. On the other hand the scanner based being a fixed size with high resolution as mentioned above will require space of approximately 150 to 160 mm over the sheet inspection area.
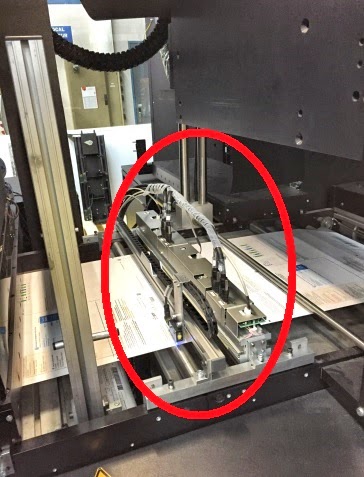
MaxScan fitted on the machine
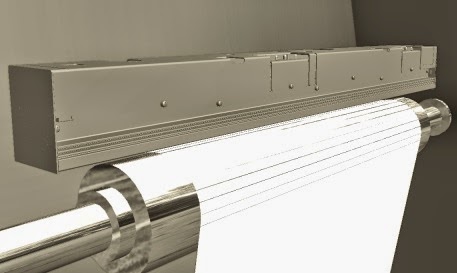
MaxScan : Distance from paper surface
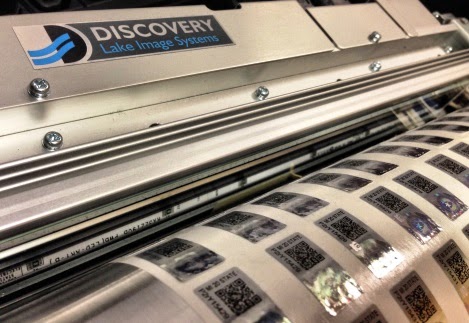
Another view
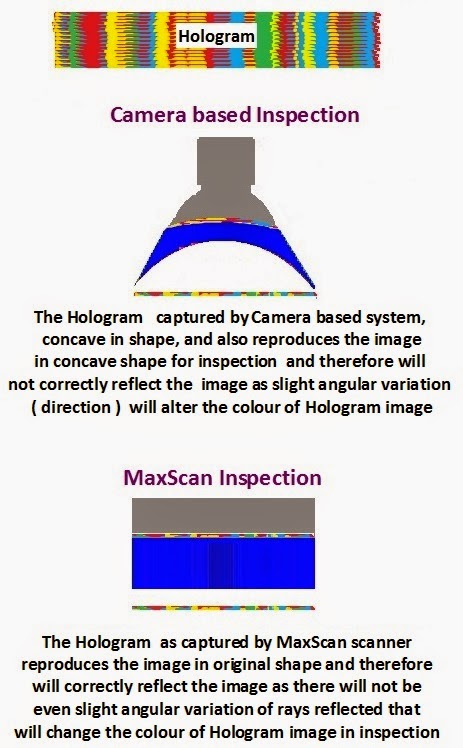
4) Since there is no angular variation from one side of the image to the other side of the image the inspection by MaxScan, the reason being short gap between scanner and sheet which is not disturbed by lighting optics, and therefore is consistent in inspection and foolproof compared to the conventional camera based system which fails to inspect the hologram based printed sheets due to the reflection arising out of lighting optics between the camera and the sheet inspected.
To my query whether MaxScan can be retrofitted on normal printing machines like Super Simultan, Orlof Intaglio for online inspection without disturbing other settings? Or is it finished sheet inspection machine done after entire sheets have been printed , Mr. Martin Keats, Managing Director informed me the following:
(1) While the Maxscan sensor (with associated inspections hardware and software) will be more expensive than a traditional camera based inspection system, there will be substantial savings with the ancillary mechanics and implementation, therefore it can prove to be more cost effective ultimately, while giving much higher inspection performance.
(2) Our technology can be retrofitted to most press technologies as an integral part of the press. We have installed our systems using the MaxScan sensor in both new presses, and also existing presses. Where possible we will try to avoid having to add additional mechanics etc. If it is sheet fed we will need to make sure the sheet is being transported in a stable and consistent fashion in the area we need to inspect.
Lake Image Systems whose invention is MaxScan has been world leader in the design, development and manufacture of imaging and scanning technologies for the worlds printing, mailing and labeling industries. Their system includes document and mail piece integrity, pin number verification, print quality inspection etc for both continuous and sheet printing, narrow web, plastic card and postal automation applications. Discovery MultiScan has standard integration packages available for virtually all brands of printing, mailing, bindery and finishing equipment.
For further info or clarification Mr Martin Keats or the firm could be contacted.
Lake Image Systems Ltd
The Forum, Icknield Way,
Tring, Herts,
HP23 4JX
UNITED KINGDOM
tel. +44 (0) 1442 892 700
fax. +44 (0) 1442 892 792
email: sales@lakeimage.com
Recent Comments