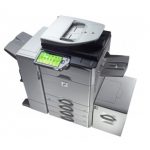
Recent developments in Printing – 4
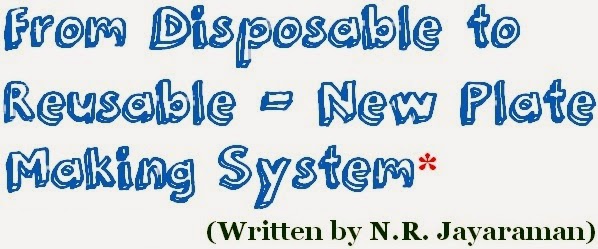
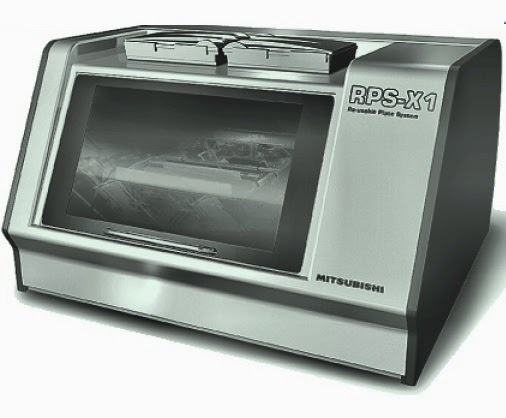
- Expensive laser imaging devices must be installed in each printing unit, making the initial investment very high.
- The printing machine must be stopped during plate making, thus lowering the production flow of the printing machine.
- Existing plates on the market for Computer to Press are higher in cost than other plates for CTP or PS.
The Plate recycling or reusable plate suggested is not meant to merely reduce the cost alone, but also to drastically reduce the annual consumption of aluminum material that overcomes one important environment hazards caused in the destruction of this metal besides reduction in material cost as the same base plate can be used repeatedly through this system.
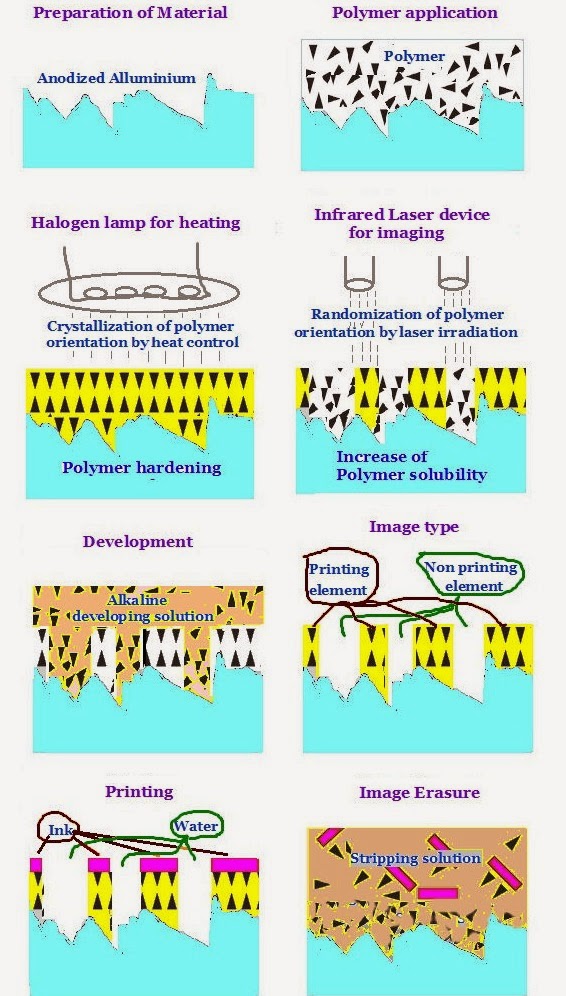
(1) Since the base metal used as print image carrier needs to have sufficient durability to withstand repeated use, an anodized aluminum plate which has excellent retention of water, with 0.1 mm to 0.3 mm in thickness can be used as base material of the Plate. Due to thinness of the metal it is likely to be deformed or flawed during transportation and therefore it is installed on a sleeve and conveyed together with the sleeve from plate making to the printing unit unlike conventional method where the plate is carried and mounted on a plate cylinder. This sleeved plate prevents deformation of flaws that could occur during transportation and ensure satisfactory print quality equivalent to the one realized with Pre Sensitized and Computer To Plate.
(2) The second is the Polymer application on this sleeved metal plate. The Polymer element is required to have print durability with control of the film strength of print images, and also ease of erasing the images for recycling. The polymer can be handled in room light, and does not require any special storage facility.
(3) The third is the heating orientation in which the Polymer is crystallized through heating with halogen lamp, and a printing area layer with excellent print durability of high hardness and very low solubility can be formed.
(4) By emitting infrared laser radiation oscillation in wavelength of 830 nm, the polymer in image area is instantly heated to a high temperature at the same time increasing the solubility of non print areas in a developer solution.
(5) The polymer in the non-printing area is dissolved and removed with alkaline solution while the image area remain unaffected thus completing the plate making process which realizes ready to use printing plate.
(6) Prints are taken in usual presses with suitable commercial ink with or without dampening water.
(7) The polymer in the printing area is also dissolved after printing with another alkaline aqueous solution used as stripping or erasing solution, in which process the polymer is stripped off from the plate surface followed by washing with normal water that removes the eraser liquid from the plate surface so that the grained surface plate as was available in initial state for coating Polymer is obtained as fresh as before. The process of re coating and eraser is repeated after completion of every print order.
(2) Imaging and developing unit and
(3) Image erasure unit
After completion of the print order the plate moves through these stations sequentially in their sleeve format, and undergoes plate making and recycling process. Each time the printing plate is sequentially processed, regenerated and processed in preset manner. The sleeved plate cylinder is formatted in such a manner that after completing printing, the plate can be detached from the sleeve in axial position and then inserted in the RPS-X1 for regeneration and recycling process. Handling of the printing plate is thus made very easy during the print and recycling process.
The printing plate can be regenerated and used repeatedly till the grain on the metal gets deteriorated due to abrasion in regeneration process. The repeated regeneration of the plate causes reduction of cost on the printing material. In order to verify the print result of the degenerated plate, prints from the plate that was regenerated and used 20 times was taken and analyzed which indicated that no deterioration was found in print quality after sample from each copy of printing were measured for changes of dot percentage.
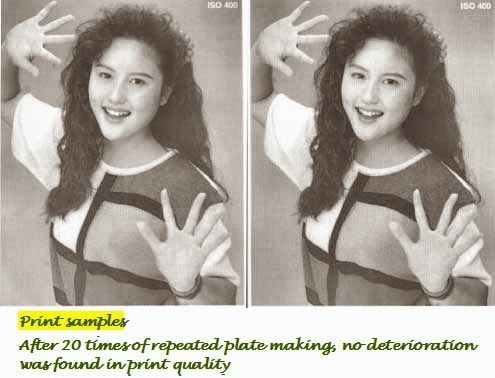
The processing devices of the RPS-X1 are installed on an elevating stage which moves up and down to accommodate various diameter sizes of sleeved plates and each processing device is set in an appropriate position to the plate surface. The conventional type of plate making device is installed in a prepress room with a relatively favorable environment. The RPS-X1 system if installed in the printing shop a clean air supply facility is required to prevent dust deposits that may emerge from the system causing plate making defects.
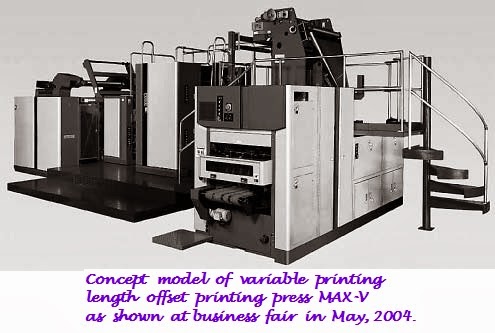
The higher version MAX-V concept machine reusable plate making system is being developed to realize a combined system for commercial web offset printing press of variable printing length.
The higher version MAX-V new Plate recycling technology ensures reduction of plate material cost and lowering of impact on the environment while maintaining level of printing productivity as the new system suites printing needs of even small lots in the present diversified applications. This system can also be effectively used in web offset printing press of variable printing length.
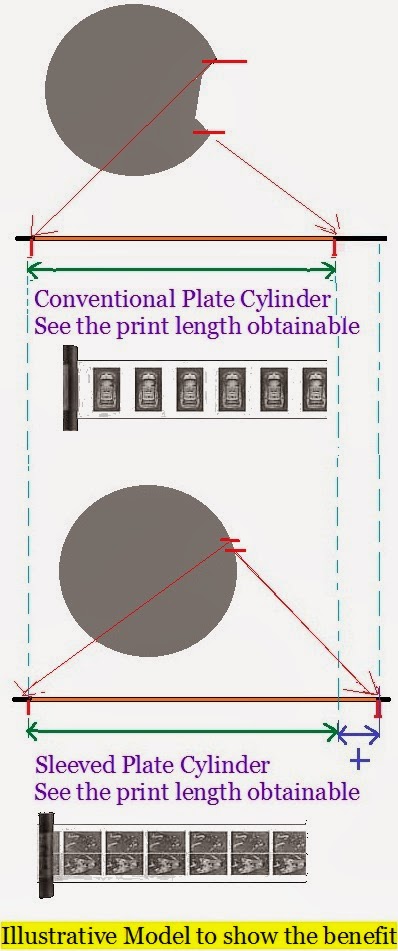
In web offset printing, the print size is limited and, depending on the size, waste of paper may be increased, but by varying the diameter of the plate sleeve, flexibility is possible with the use of full length plate without leaving much margin for the fixing bars as the plate is in sleeve format. As a result, one printing press can handle printing jobs of multiple sizes, and waste of paper is reduced.
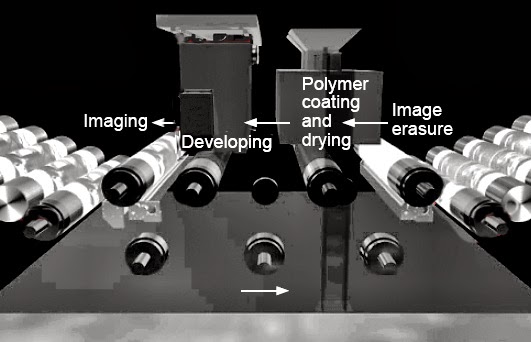
The reusable plate system is applicable to changes in plate sleeve diameter, and in a system combined with MAX-V, waste is eliminated and running costs are reduced substantially. The concept machine RPS-X1 is designed to make plates sequentially, but an effective method of improving the processing speed is to make plates simultaneously in parallel processes. This is also realized by the multi cylinder system shown above.
(*)
Mitsubishi Heavy Industries
1-1, Itosaki Minami 1-chome,
Mihara,
Hiroshima,
729-0393,
Japan
Phone: +81-848-67-2068
Technical Review|Mitsubishi Heavy Industries, Ltd, http://www.mhi.co.jp/en/technology/review/indexe-42-2.html
3) If only one machine could print in various sizes!” The answer to such a market need is the newly developed variable size commercial web offset press LITHOPIA MAX-V. In a commercial web offset press, since continuous paper is used, high-speed operation is possible and its productivity is more than three times that of the sheet fed press. It has thus been a dream of the printing industry to realize flexibility of its print size, overcoming all difficulties to meet the high expectations held for such technology. Mitsubishi Heavy Industries, Ltd. (MHI) has developed “LITHOPIA MAX-V,” a variable size commercial web offset press, which allows easy replacement of major component parts such as the plate cylinder. The printing cylinder has a sleeve mounted on the core so that the cylinder’s circumferential length can be changed by replacing the sleeve, enabling the printing size to be changed. The first product was delivered to a domestic printing company and started commercial operation at the end of October 2005. {Courtesy : Mitsubishi Heavy Industries, Ltd.Technical Review Vol. 43 No. 3 (Sept. 2006)}
Recent Comments