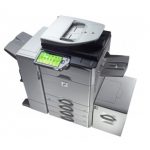
Alphabet- S /3
13. Slurring: This is one of the most commonly seen printing defect in Offset printing. Specially while printing halftone images, the occurrence of slurring is seen to be more. The problem could be due to
- The blanket becomes slightly loos
- The paper slips at the end of the impression
- The pressure between the plate cylinder and the blanket cylinder or between blanket cylinder with impression cylinder is heavy etc.
- If the paper is wavy, it can also cause this defect.
This is another form of doubling we can say. How will Slur look like? It will be a blurred image or a ghost image that causes the dots to enlarge due to pressure. The edges of the enlarged dots will also be not sharp.
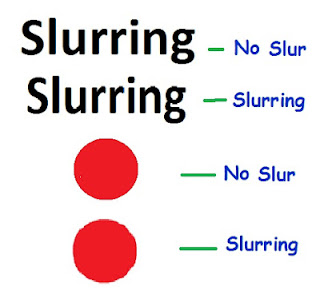
14. Smashed blanket:- Sometimes during machine run, some extraneous particles may come in between the blanket and the plate or the impression cylinder and damage the blanket. Some times the paper with fold when unknowingly fed causes this problem. In such cases the blanket will not produce the print properly as the impression at that point may not be proper and print will show weak image on that spot. Such blankets are known as Smashed Blankets.
They can however be partially repaired by under packing the blanket at that particular spot or treat the blanket with some solution to swell the area to regain its thickness since the Offset blankets are made of layers of rubber and fabric in between. When the number of rubber layer is more on the blanket, the chances of it getting smashed will be much less as the rubber has elasticity to compress and regain its surface like a sponge.
15. Spiral or special cut rollers : This will have relief surface on the image areas which will be slightly bigger than the image. The cut portions on the roller will not be exactly like the image , but will have only a solid rubber block to ink the image. There are two varieties of such rollers. One roller is with intermediary relief cut regular rollers, and the other is specific cut to suit the design element (See illustration to understand this) .
Generally the ink supply to the rollers which supply them to the plate is controlled with separators or dividers or the control keys in the ink duct. For certain other process of printing, special rollers are used. They are called Spiral Cut or Special Cut Rollers whose surface will be in relief in the image areas. Depending upon the requirement of ink to be fed, the roller surface is cut at image inking points to feed ink only to the particular area (like Engraved roller ). This type of rollers are mostly employed where the job is regular running job of the same image in nature, or the volume of print is much higher. Example match box labels, Cigarette labels, other consumable product standard labels etc. The Special Cut Rollers cuts down the consumption of ink considerably and also prevent non image areas causing technical problem (See illustration to understand the term) .
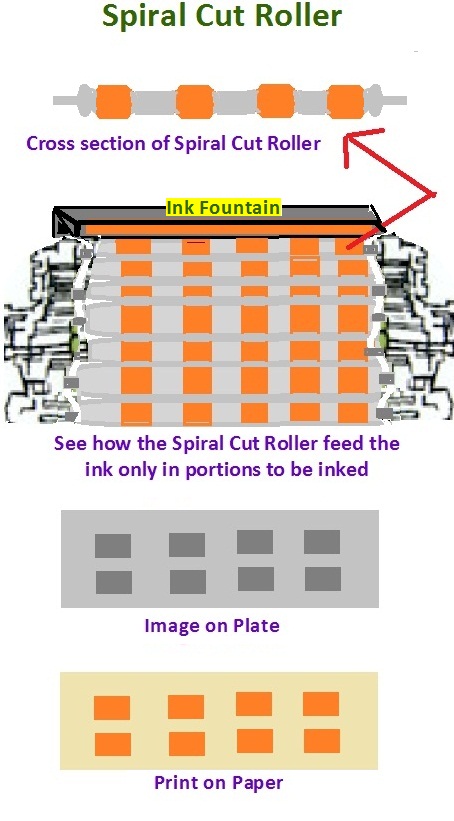
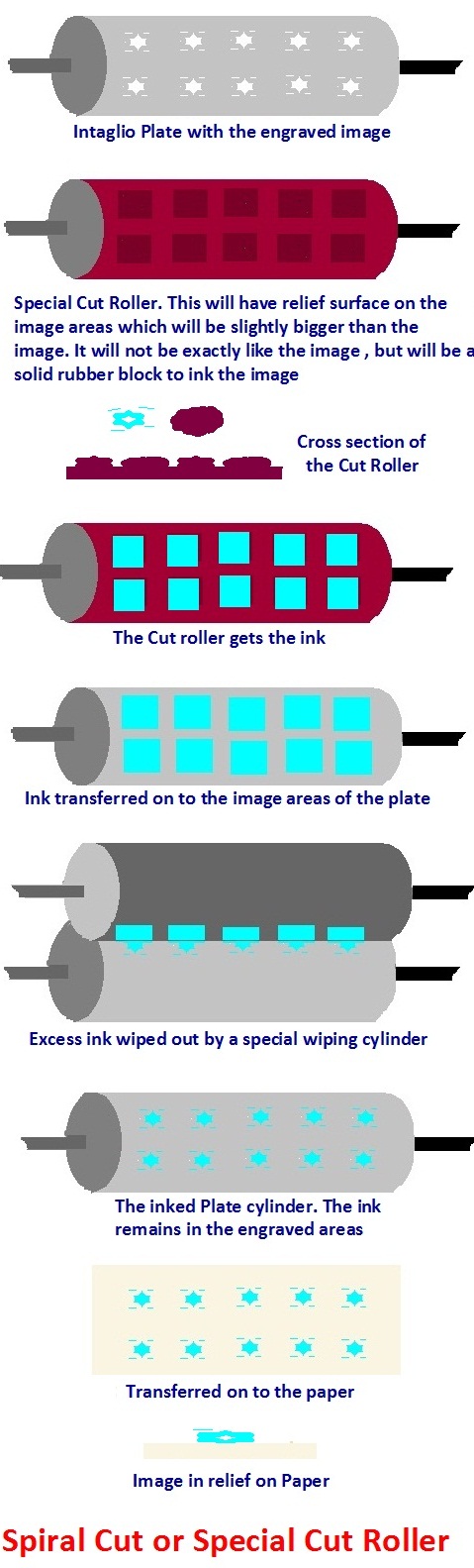
16. See through image: This is a special technique employed in high security printing like printing of Currency notes and possible only on perfecting presses where the recto verso sides of the paper is printed simultaneously. See through means elements of a design are printed on both sides of the sheet in perfect register so that when the sheet is held against light the complete design can be seen. How this is achieved? The floral design to be printed will be split into two halves and each halve printed on either side of the paper in such a position that when the sheet is held against light, the two halves of the images will show as a complete image in perfect register without disjoint. This is very difficult to achieve when the sheets are printed on one side and then printed again on the reverse side.
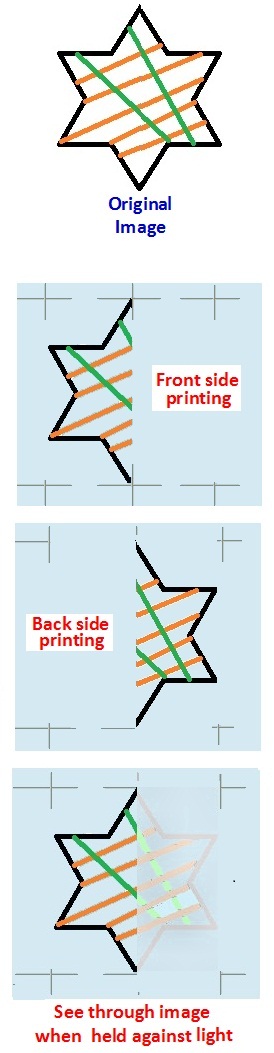
Recent Comments